Are you looking to learn how to weld cast iron with TIG? Wielding cast iron is not as difficult as it may seem, and once you understand the process, you can quickly complete your project in no time.
For those new to casting, it can be intimidating at first – welding cast iron requires some knowledge and skill, but with the right tools and techniques, anyone can become an expert welder!
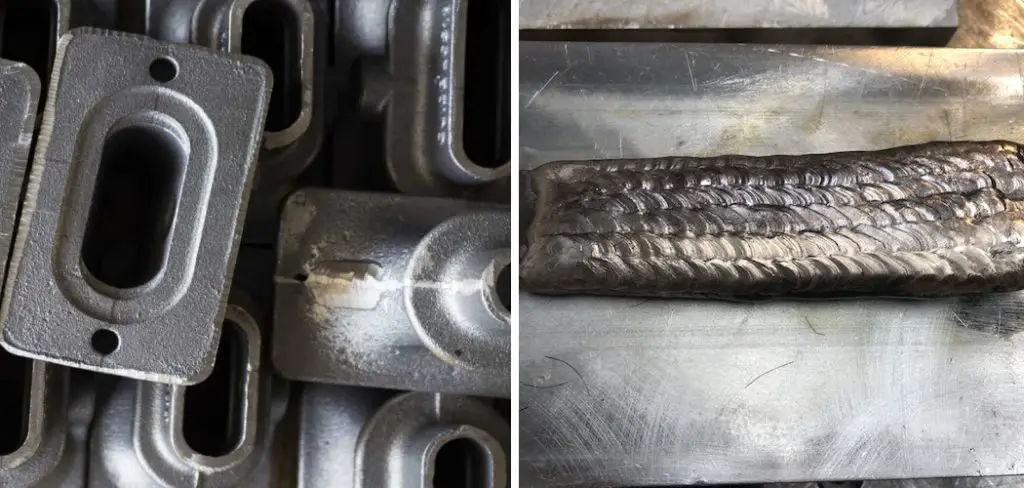
Cast iron is a strong and durable material that is commonly used in various industries. It has excellent heat retention properties, making it ideal for engine blocks, manifolds, and machine parts applications.
In this blog post, I will explain the basics of weld cast iron with TIG welding so that even newcomers will have all they need for success!
What Will You Need?
Before we dive into the process, make sure you have all the necessary tools and equipment:
- Tungsten inert gas (TIG) welding machine
- Filler metal rods suitable for cast iron
- Argon gas cylinder for shielding
- Welding gloves, helmet, and other safety gear
- Wire brush and grinder for cleaning the casting surface
- Vise grips or clamps to hold the parts in place
Once you have all of these items, you are ready to begin!
8 Easy Steps on How to Weld Cast Iron With TIG
Step 1. Preparation of the Cast Iron:
The first step is to thoroughly clean the cast iron surface you will be welding. Use a wire brush or grinder to remove any rust or dirt. This ensures a smooth and clean surface for welding. If there are any cracks in the material, drill stop holes at the end of them to prevent further spreading. This step is crucial as contaminants can adversely affect the weld quality.
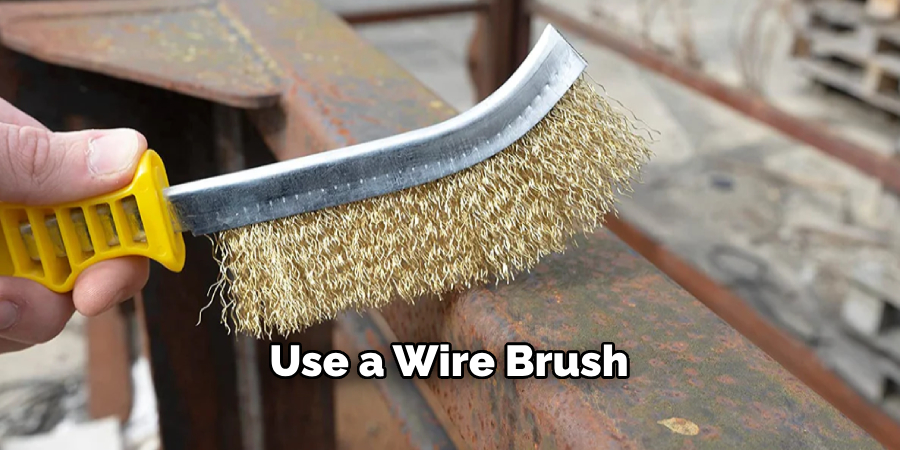
Step 2. Preheat the Cast Iron:
Before you can begin welding, preheating the cast iron is critical. This material is susceptible to crack formation due to rapid heating and cooling, so gradual and uniform preheating is crucial.
This can be done using a torch or oven, heating the cast iron to a temperature between 500 to 1200 degrees Fahrenheit (260 to 650 degrees Celsius). Remember, the goal is to reduce the temperature difference between the welding arc and the base metal, minimizing thermal shock. After preheating, maintain the temperature throughout the welding process using a temperature stick or infrared thermometer to monitor.
Step 3. Set Up the TIG Welder:
After preheating, you will need to set up your TIG welder correctly. This process involves selecting the right electrode, typically a non-consumable tungsten electrode, and setting the correct amperage on the machine.
The amperage should be set based on the thickness of the cast iron. A good rule of thumb is to use 1 amp for every 0.001 inch of material thickness. Also, ensure the argon gas shielding is set up correctly to protect the weld pool from contaminants in the atmosphere.
Step 4. Begin the Welding Process:
Now that everything is set up, you can begin welding. Start by striking the arc on the cast iron piece using the TIG torch. Ensure a short arc length to ensure a stable arc and better control. As you move the torch along the joint, dip the filler rod in and out of the weld pool to deposit the filler metal.
The motion should be steady and coordinated; remember to let the weld pool cool slightly before adding more filler material. This helps to maintain the integrity of the weld and prevents overheating of the cast iron.
Step 5. Maintain a Slow Welding Speed:
It’s important to maintain a slow and steady welding speed when working with cast iron. This is because cast iron doesn’t melt as quickly as other metals. Hence, a slower rate ensures that the heat is evenly distributed, reducing the risk of overheating and potential cracking.
Always aim for a consistent speed that allows for a steady filler metal deposit. The welding speed will also depend on the cast iron’s thickness and the weld joint’s specific design.
Step 6. Let the Weld Cool Naturally:
Once you’ve completed the welding, allowing the cast iron to cool naturally is critical. Rapid cooling can lead to thermal shock, which can cause the weld to crack.
Some welders prefer to wrap the welded piece in an insulating blanket to slow the cooling process. This practice, known as “post-weld heat treatment,” can help prevent the formation of brittle and hard zones in the weld area.
Step 7. Inspect the Welded Joint:
Once the cast iron piece has cooled down completely, it’s time to inspect your work. Look for any signs of cracks or imperfections in the weld. A well-done weld should show good fusion between the base and filler metals. Perform a visual inspection to ensure the weld seam is uniform and free from defects.
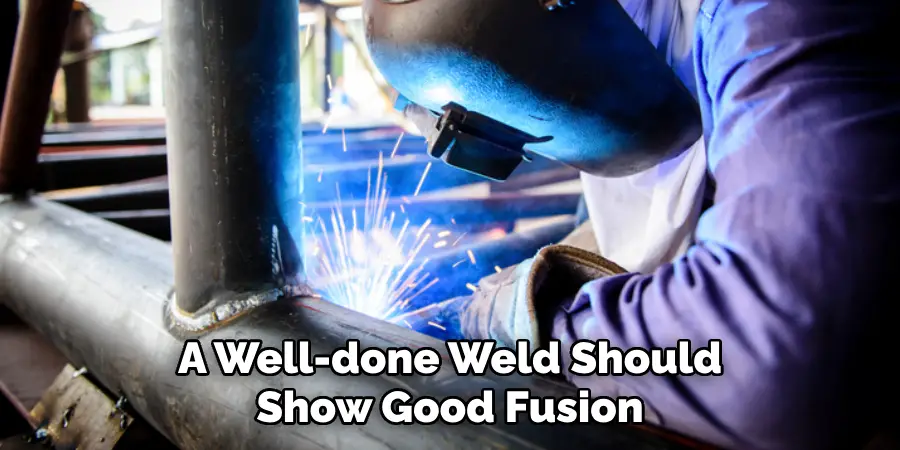
You can also utilize non-destructive testing methods, such as dye penetrant testing, to detect hidden cracks or faults. If you find any issues, you should grind out the flawed area and re-weld it.
Step 8. Post-Weld Cleanup:
Once you’re confident about the quality of your weld, the final step is post-weld cleanup. Use a wire brush to remove any slag or excess filler material from the weld seam. If necessary, a grinder can be used for smoothing the surface. Remember, the goal of this step is to ensure the repaired cast iron component appears as seamless and professional as possible.
Finally, apply a coat of paint or protective finish to prevent the formation of rust and further enhance the longevity of the repair. With this step, you have completed the process of welding cast iron with TIG!
Following these easy steps, you can effectively repair damaged or broken cast iron components using TIG welding. Remember that practice makes perfect, and it may take a few attempts to get comfortable with the process.
5 Additional Tips and Tricks
Tip 1. Choosing the Right Filler Metal:
Choosing the right filler metal is pivotal for successful TIG welding of cast iron. Nickel-based rods are a popular choice due to their ability to reduce the formation of brittle iron carbides in the weld.
Tip 2. Don’t Rush the Preheating Process:
As mentioned earlier, preheating is critical when welding cast iron. Take your time to ensure that the material has reached the recommended temperature before starting the welding process.
Tip 3. Weld in Small Sections:
To reduce heat buildup and prevent thermal shock, it’s best to weld cast iron in small sections. This allows for better control and ensures that the weld is evenly distributed.
Tip 4. Be Mindful of the Welding Position:
The welding position can significantly affect the success of your TIG welding on cast iron. It’s best to weld in a flat or slightly inclined position, as this provides better access to the joint and reduces heat buildup.
Tip 5. Consider Using a Backing Plate:
For thicker cast iron pieces, using a backing plate can help prevent distortion and improve the overall quality of the weld. The backing plate should be made of copper or steel, with a thickness similar to that of the cast iron being welded. It’s placed behind the joint to absorb excess heat and prevent warping.
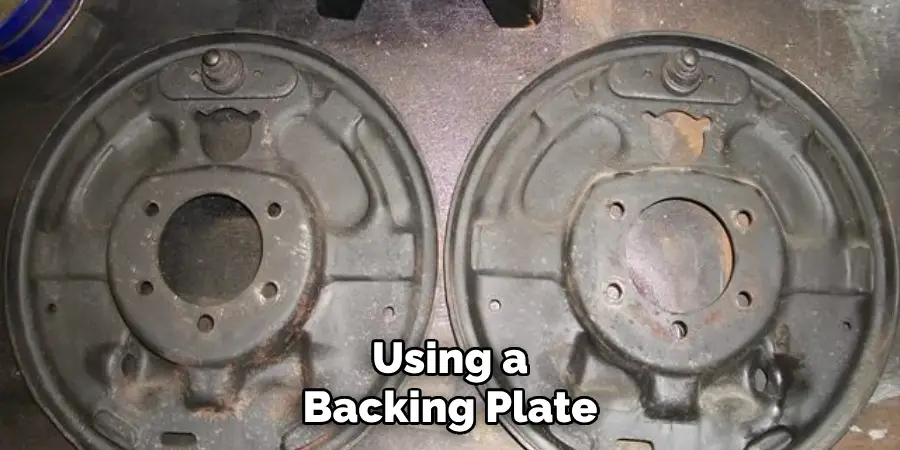
With these additional tips and tricks, you can confidently tackle your next TIG welding project involving cast iron.
5 Things You Should Avoid
Avoid 1: Skipping the Preheating Stage:
Pay attention to the preheating stage when welding cast iron. Skipping this crucial step can result in thermal shock, causing the cast iron to crack due to rapid expansion and contraction.
Avoid 2: Avoid Rapid Cooling:
As mentioned earlier, rapid cooling can cause thermal shock and cracks in the weld. Avoid using any forced cooling methods or submerging the cast iron in water immediately after welding.
Avoid 3: Using the Wrong Amperage:
Using too much or too little amperage can negatively impact the quality of your TIG weld on cast iron. Refer to the manufacturer’s recommended settings for the specific type and thickness of cast iron you’re working with.
Avoid 4: Not Using Proper Eye and Skin Protection:
TIG welding produces intense light that can damage your eyes if not appropriately protected. Always wear a welding helmet with a shade appropriate for TIG welding and protective clothing to shield your skin from UV radiation and sparks.
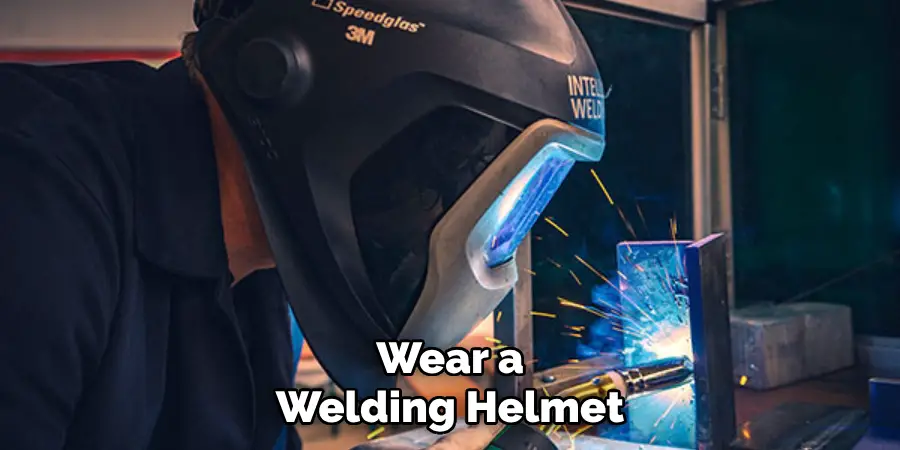
Avoid 5: Welding Near Flammable Materials:
TIG welding produces high heat and sparks, making it important to clear your work area of any flammable materials. Failure to do so can result in fires or other hazards.
By avoiding these common mistakes, you can ensure the safety and success of your TIG welding project on cast iron.
Conclusion
With all of this helpful information on how to weld cast iron with TIG, it’s time to get started and create the beautiful metal sculptures that you have been dreaming about.
Whether you are an amateur metal worker or a professional welder, welding cast iron with TIG can help open up possibilities across various projects. Remember to take the necessary safety precautions and wear protective equipment to ensure the best possible outcome for your welds.
Finally, have patience. Practice is key, and always encourage yourself to take on new projects – you never know what kind of unique design you’ll be able to dream up when working with cast iron! So, go get started on your project today!
Edmund Sumlin is a skilled author for Metal Fixes, bringing 6 years of expertise in crafting a wide range of metal fixtures. With a strong background in metalwork, Edmund’s knowledge spans various types of fixtures, from decorative pieces to functional hardware, blending precision with creativity. His passion for metalworking and design has made him a trusted resource in the industry.
Professional Focus:
- Expert in Metal Fixtures : Edmund aesthetic specializes in creating durable and innovative metal fixtures, offering both appeal and functionality. His work reflects a deep understanding of metalworking techniques and materials.
- Sustainability Advocate : He is dedicated to using sustainable practices, ensuring that every fixture is crafted with eco-friendly methods while maintaining high-quality standards.
In his writing for Metal Fixes, Edmund provides valuable insights into the latest trends, techniques, and practical advice for those passionate about metal fixtures, whether they are professionals or DIY enthusiasts. His focus on combining artistry with engineering helps others discover the true potential of metal in design.