Are you looking to tackle a DIY exhaust repair without a welding kit? Welding may seem intimidating, but fear not – it isn’t as daunting as it appears. While welding is the preferred method for working with metal pipes, there are some ways by which you can stick and join your exhaust pipe together without a welder.
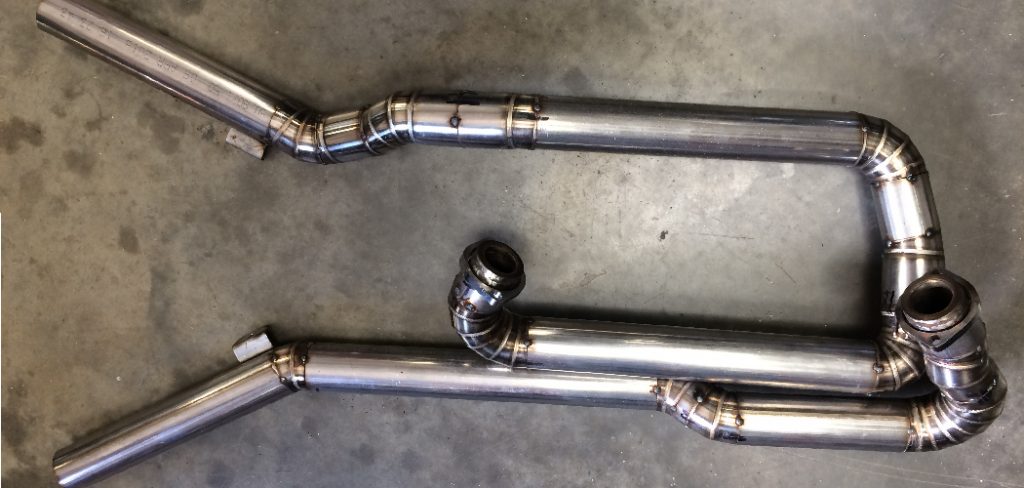
Whether you are on a tight budget or don’t have access to a welder, this guide will provide you with some practical and easy techniques on how to weld exhaust pipe without a welder.
In this blog post, we’ll explore what tools and materials are needed to weld pipe without relying on costly equipment or professional help! We’ll also go over safety tips so that you don’t damage yourself or anything else in the surrounding area while carrying out this project.
What Will You Need?
Before starting any DIY project, gathering all the necessary tools and materials is essential. For welding exhaust pipes without a welder, you’ll need:
- A pipe cutter or hacksaw
- Pipe clamps
- Metal adhesive
- An angle grinder with sanding discs
- High heat-resistant epoxy
Additionally, wear protective gear like gloves, eyewear, and a mask to prevent any potential injuries.
9 Easy Steps on How to Weld Exhaust Pipe Without a Welder
Step 1. Measure and Mark:
Start by measuring the area of the pipe you want to join and mark it accurately. This is where you will make the cut or join, depending on what you are trying to achieve. If it’s a damaged area, mark the extent of damage.
Step 2. Cut or Remove Damaged Area:
After marking, use a pipe cutter or a hacksaw to cut off the damaged area of the pipe. Ensure to cut smoothly and avoid making jagged edges, as they can make the joining process more difficult. If you’re not removing a damaged part but joining two pipes, skip this step.
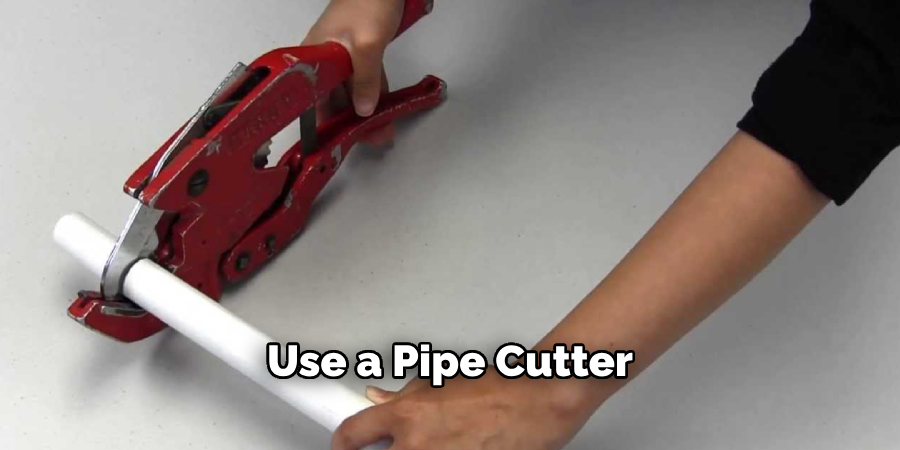
Step 3. Prepare the Pipe Surfaces:
Once the damaged part has been removed or the pipes to be joined are ready, it’s time to prepare the surfaces. Use an angle grinder with a sanding disc to clean and smooth the ends of the pipes. This is crucial as it helps to ensure a firm grip when applying the adhesive and makes the bonding process more effective. Be careful while using the angle grinder, and wear your protective gear.
Step 4. Apply the Metal Adhesive:
Now that the pipe surfaces are prepared, it’s time to apply the metal adhesive. The adhesive will act as a bonding agent between the two pipes, effectively “welding” them together. Apply a generous amount of adhesive on both ends of the pipes to be joined, but ensure it is spread evenly.
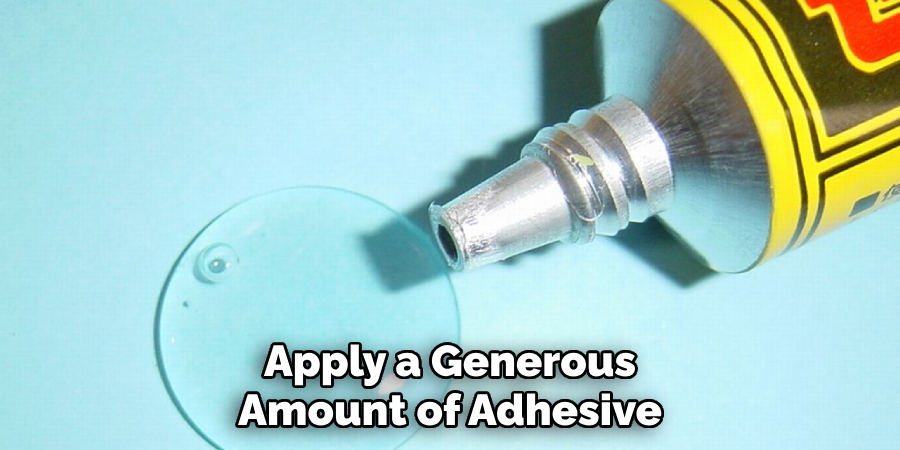
You don’t want it to be too thick as it might not dry properly, but also not too thin as it might not provide enough grip. After applying the adhesive, join the pipes together and hold firmly for a few seconds to allow the glue to take hold.
Step 5. Secure the Joint with Pipe Clamps:
After the adhesive has taken hold, use pipe clamps to secure the joint further. Place one clamp at either end of the joint, tightening them until they are firm but not overly tight so as to deform the pipe.
These clamps will support the joint while the adhesive dries completely, which can take several hours, depending on the specific product you’re using. It’s essential to leave the clamps in place until the adhesive is fully cured to ensure the best possible bond.
Step 6. Apply High Heat-Resistant Epoxy:
Once the adhesive has fully cured, it’s time to apply the high heat-resistant epoxy. This step is vital as the exhaust pipe will be exposed to high temperatures, and standard adhesive might not withstand the heat. Apply the epoxy evenly over the joint, ensuring it covers all areas and fills gaps.
This not only reinforces the joint but also helps to seal it, preventing any possible exhaust leaks. Like with the adhesive, it’s essential to give the epoxy sufficient time to dry and cure fully before moving on to the next step.
Step 7. Check for Leaks:
After the epoxy has thoroughly dried, it’s time to check for any potential leaks. Start your vehicle and listen carefully for any unusual sounds that could indicate a leak, such as hissing or popping. You can feel around the joint for any air escaping, but be cautious as the exhaust pipe can get extremely hot.
If you discover a leak, you may need to apply more epoxy or adhesive and repeat the process. Congratulations if there are no leaks – you’ve successfully welded an exhaust pipe without a welder!
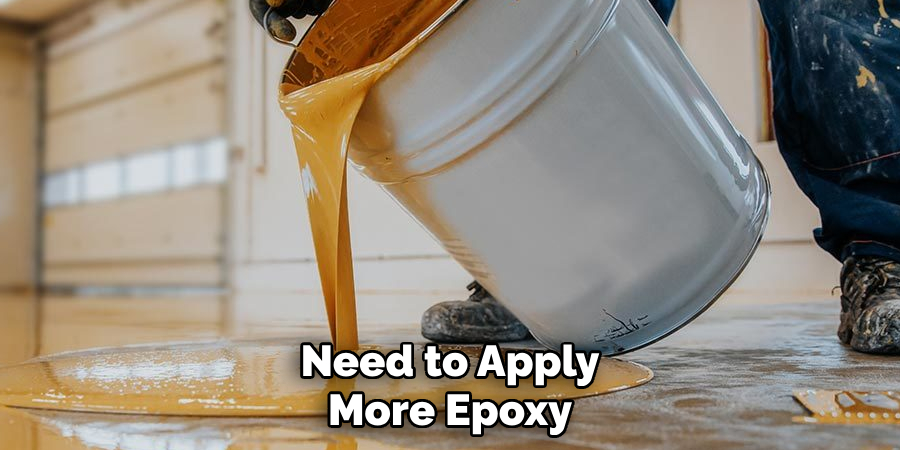
Step 8. Finish and Polish:
Now that your pipe is effectively sealed and checked for leaks, the final step is to finish and polish the exhaust pipe. Carefully smooth out the joint area using your angle grinder and a suitable polishing disc.
This step will help to blend the joint with the rest of the pipe, making it less visible and giving it a professional finish. Remember to wear your protective gear while handling the grinder. Once done, your exhaust pipe should look as good as new, and you can be proud of completing this task without needing a welder!
Step 9. Regular Maintenance:
After successfully welding your exhaust pipe without a welder, it’s crucial to maintain it properly to ensure its longevity. Regular inspections for potential leaks or damage is a good practice. Also, cleaning the pipe occasionally can prevent dirt or debris buildup that might cause future issues. By taking these preventative measures, you can ensure that your exhaust pipe stays in good condition for a long time.
By following these simple steps, you can save time and money by welding your exhaust pipe without a welder.
5 Additional Tips and Tricks
- Use Exhaust Clamps: If you’re looking for a quick fix and don’t have a welder, using exhaust clamps can be an excellent solution. These clamps work by sealing the joints, preventing exhaust leaks.
- Heat Resistance: Consider using heat-resistant epoxy to fix small holes or leaks in the exhaust pipe. It’s a simple solution that requires no welding. Just make sure to let the epoxy fully cure before running the engine.
- Pipe Patching: You can patch larger holes using an aluminum patch and high-heat adhesive. This method is more temporary than others but can hold until you can get the pipe replaced or welded.
- Regular Maintenance: Regularly inspect your exhaust system for signs of wear and tear. Catching problems early can prevent the need for significant repairs.
- Keep a Welding Kit on Hand: If you often need to weld exhaust pipes, consider investing in a welding kit designed for exhaust systems. These kits are affordable and can save you time and money in the long run.
With these additional tips and tricks, you can confidently tackle any exhaust pipe issues without a welder.
5 Things You Should Avoid
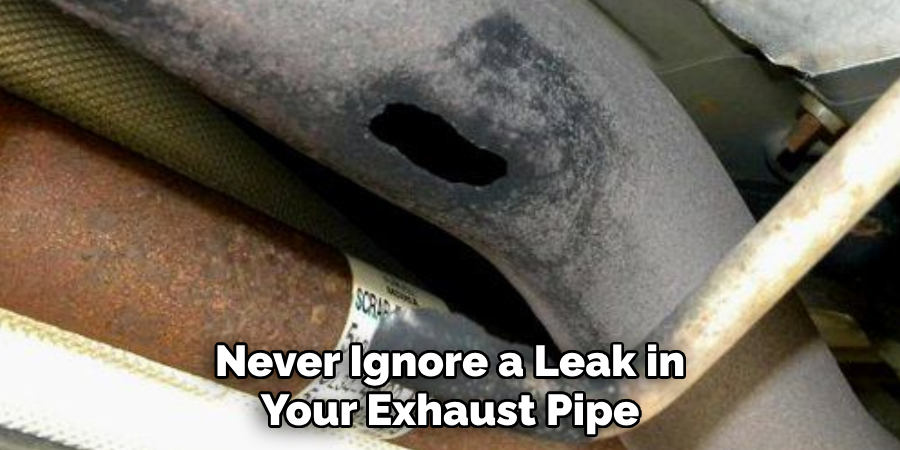
- Avoid Ignoring Leaks: Never ignore a leak in your exhaust pipe. Even a tiny leak can lead to more significant problems, including decreased fuel efficiency and potential damage to other exhaust system parts.
- Avoid Using the Wrong Materials: Avoid using materials not heat-resistant for patching. They may not withstand the high temperatures of the exhaust system and could lead to further damage.
- Avoid Rushing the Repair: Do not rush to fix your exhaust pipe without adequately checking the extent of the damage. A hasty repair can lead to more problems in the future.
- Avoid Skipping Safety Measures: Never skip safety measures while working on your exhaust pipe, even if you’re not using a welder. Always wear protective gloves and glasses, and work in a well-ventilated area.
- Avoid Continuous Temporary Fixes: While temporary fixes can be helpful, continuously relying on them instead of seeking a permanent solution can lead to more significant issues. Always aim to replace or professionally repair the exhaust pipe when it’s feasible to do so.
By avoiding these common mistakes, you can ensure that your exhaust pipe stays in good condition and avoid any potential hazards or costly repairs.
Conclusion
In conclusion, how to weld exhaust pipe without a welder is more than possible with suitable materials and techniques. With this knowledge, you can tackle small repairs on your own and save yourself some money.
Carefully analyze the scope and size of your project to determine if it’s within your capabilities, and read up on resources to ensure that you are doing the job safely. When tackling these projects, remember to proceed slowly and take all safety precautions necessary. For bigger jobs, getting a professional may be safer for your vehicle in the long run.
So, whatever project or repair you have in mind, remember that welding exhaust pipes without a welder aren’t as rigid as they may have seemed when first encountered. Armed with just a few supplies and an understanding of the process, welding exhaust pipes can be pretty enjoyable – just always stay safe!
Edmund Sumlin is a skilled author for Metal Fixes, bringing 6 years of expertise in crafting a wide range of metal fixtures. With a strong background in metalwork, Edmund’s knowledge spans various types of fixtures, from decorative pieces to functional hardware, blending precision with creativity. His passion for metalworking and design has made him a trusted resource in the industry.
Professional Focus:
- Expert in Metal Fixtures : Edmund aesthetic specializes in creating durable and innovative metal fixtures, offering both appeal and functionality. His work reflects a deep understanding of metalworking techniques and materials.
- Sustainability Advocate : He is dedicated to using sustainable practices, ensuring that every fixture is crafted with eco-friendly methods while maintaining high-quality standards.
In his writing for Metal Fixes, Edmund provides valuable insights into the latest trends, techniques, and practical advice for those passionate about metal fixtures, whether they are professionals or DIY enthusiasts. His focus on combining artistry with engineering helps others discover the true potential of metal in design.