Are you interested in learning how to weld Inconel, one of the most challenging and most durable alloys available? Whether you’re a professional or just getting started, soldering Inconel can be challenging. While understanding some principles of alloy metallurgy is essential for successful welding, knowing the proper techniques makes it much more manageable.
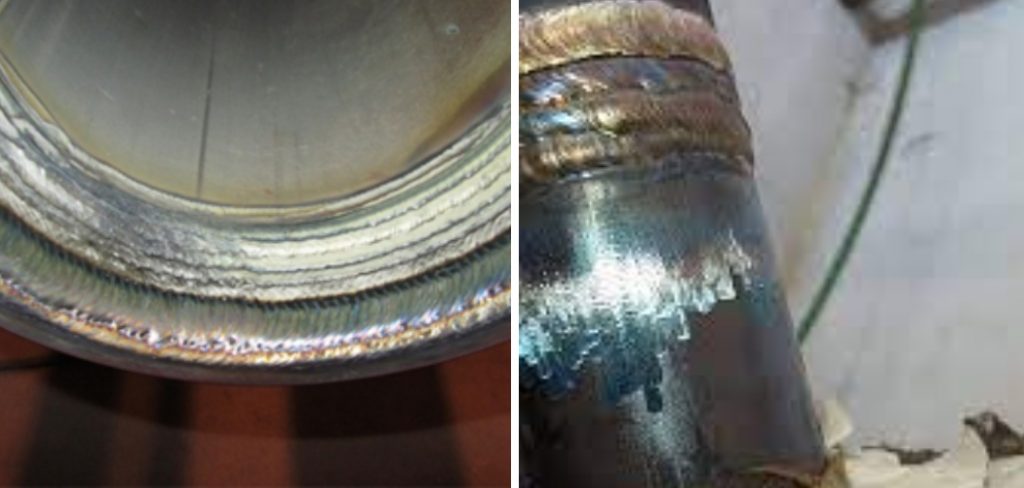
Inconel is a nickel-chromium-based alloy that offers excellent resistance to corrosion, high temperatures, and extreme environments. Due to its unique properties, Inconel is commonly used in aerospace, chemical processing, and marine industries. Welding Inconel can be tricky due to its high melting point and tendency to form a hardened layer during welding.
In this blog post, we’ll explore critical tips and tricks that will help you how to Weld Inconel in no time! From proper safety practices to choosing suitable filler metals – let’s dive into what it takes to weld like a pro!
What Will You Need?
Before we delve into the welding techniques, let’s ensure you have all the necessary tools and materials.
- Inconel filler metal (e.g. ERNiCrMo-3)
- TIG or MIG welding equipment
- Clean stainless steel wire brush
- Argon gas and flowmeter
- Protective gear (helmet, gloves, apron)
- Grinder
Once you have everything ready, it’s time to start welding!
8 Easy Steps on How to Weld Inconel
Step 1. Preparation:
Start by cleaning the surface of the Inconel. Any grease, dirt, or other contaminants can interfere with welding. Use your stainless steel wire brush to clean the area where you will be welding thoroughly. Don’t forget to put on your protective gear before starting the welding process. This includes a welding helmet, gloves, and apron. Safety should always be paramount.
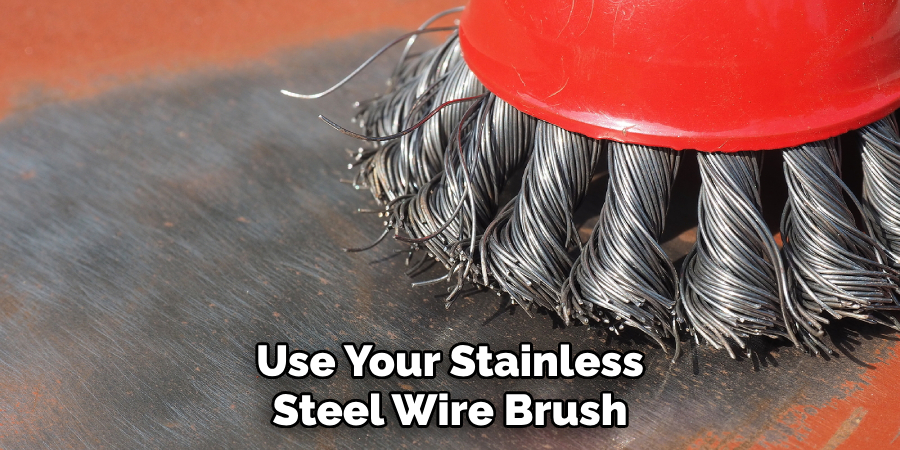
Step 2. Setting Up the Welding Machine:
Set up your welding machine according to the manufacturer’s instructions. The choice between TIG (Tungsten Inert Gas) and MIG (Metal Inert Gas) welding will depend on your particular needs and proficiency. TIG welding is generally preferred when welding Inconel due to its precision.
Set your power supply to DCEN (Direct Current Electrode Negative). Remember, the welding machine settings may vary depending on the thickness of the Inconel. For Inconel, a typical range might be between 90-120 amps for TIG welding. Ensure your flowmeter is set to provide the appropriate amount of argon gas to maintain a clean weld puddle.
Step 3. Start Welding:
Once your setup is complete, you can begin welding. Light your torch and hold it at around a 15-20 degree angle from the Inconel. This angle allows for better control of the weld pool. Begin by creating a small weld pool on the surface of the Inconel. Slowly add the filler metal to the pool, keeping the torch steady along the seam. Keep the heat and speed consistent throughout the process, as consistency could lead to a strong weld.
Patience is vital when welding Inconel because of its high melting point. If you rush the process, you might have a poor quality weld. As you finish your weld, slowly pull the heat away to avoid creating a crater, which can lead to cracking. Lastly, always allow the welded piece to cool naturally. Fast cooling methods can cause stress and potential cracks in the weld.
Step 4. Post-Welding Clean-Up:
After you’ve completed your weld and the piece has cooled naturally, it’s time to clean up the finished product. Use your grinder to smooth any rough areas on the weld. Then, use a clean stainless steel wire brush to remove any remaining oxide layer from the surface of the Inconel.
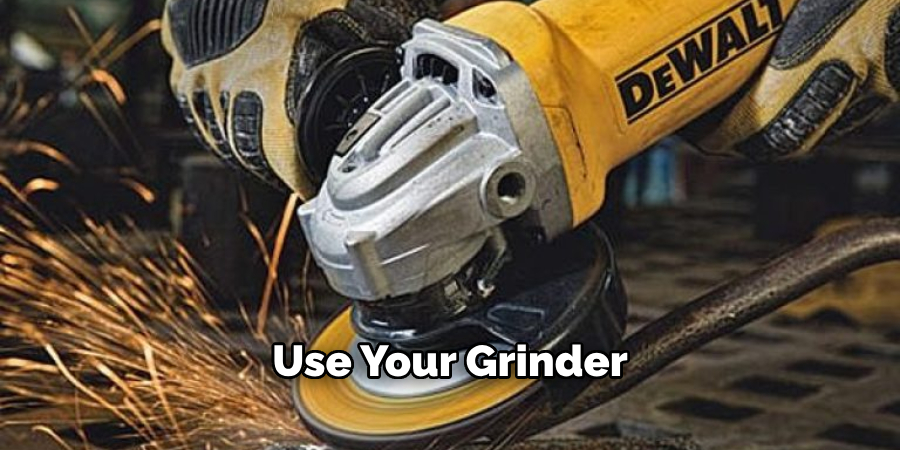
This step is crucial as it helps improve the weld’s appearance and prevents any surface contaminants from interfering with subsequent welding or other operations. Remember to wear your protective gear during this step to protect yourself from sparks and other potential hazards.
Step 5. Inspection:
Once your weld has cooled and you’ve finished the clean-up process, it’s time to inspect the weld thoroughly. Check for any apparent signs of imperfections, such as cracks, pits, or porosity. The weld should appear shiny, even, and smooth. Any inconsistencies could indicate a problem with your welding technique or settings.
If you do find any flaws, it’s important to grind them out and re-weld the area. Never leave a faulty weld, as it can lead to structural failures. Inconel welds can be more prone to cracking than other materials, so inspect carefully. It’s always best to fix any issues early on to ensure a long-lasting, reliable weld.
Step 6. Practice Makes Perfect:
Welding Inconel is indeed a challenging task, even for experienced welders. It requires patience, steady hands, and a keen eye for detail. The more you practice, the more familiar you will become with how Inconel behaves under the torch, and the better your welds will become.
Start with small, simple projects and gradually work up to more complex ones. Remember, it’s okay to make mistakes; they are part of the learning process. With practice, you’ll soon be able to achieve clean, strong welds when working with Inconel.
Step 7. Constant Learning and Adaptation:
In the world of welding, new techniques and technologies are constantly being developed. Keep yourself updated about these advancements. Attend workshops, read industry journals, participate in online forums, and watch tutorial videos. Learning from the experiences of other welders can provide invaluable insights.
Additionally, understand that different types of Inconel may behave differently under the torch, so it’s essential to do your research if you’re working with a kind of Inconel that’s new to you. Remember, successful welding of Inconel doesn’t end with mastering the basics; it is an ongoing effort to enhance your skills and adapt to new circumstances.
Step 8. Troubleshooting:
While welding Inconel, you may encounter some common issues, such as warping, cracking, or porosity. Keep going. These problems often have simple solutions. For instance, if you notice cracking, you may be cooling the weld too quickly. Try letting it cool naturally next time. If you see signs of porosity, your shielding gas flow may be insufficient, or there might be contamination on the material’s surface.
Double-check your gas settings and make sure your Inconel is clean before welding. If you face warping, it could be because your heat input is too high. Adjusting your welding machine settings can help address this issue. Remember, troubleshooting is a normal part of the learning process. Over time, you will learn to anticipate and prevent these issues, enhancing the quality of your welds.
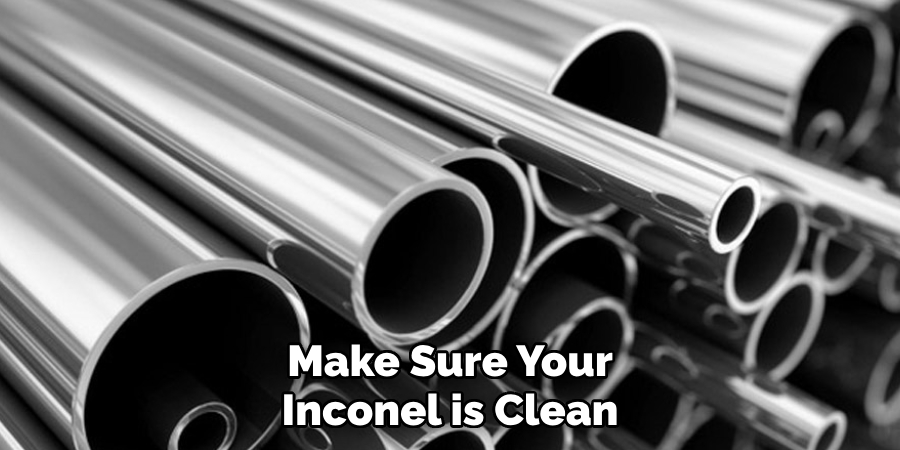
By following these steps, you can become proficient in welding Inconel. Always prioritize safety and take your time to achieve the best results.
5 Additional Tips and Tricks
- Pre-cleaning: Always ensure the Inconel is clean before you start welding. This involves removing any grease, dirt, or oxides that may be present. A clean surface helps achieve a high-quality weld.
- Use the suitable filler material: Using the appropriate filler material is crucial, depending on the type of Inconel you are welding. For instance, Inconel 625 is the filler material when welding Inconel 718.
- Control heat input: Inconel retains heat longer than other materials, which can lead to warping or cracking. Therefore, controlling the heat input during welding is essential to prevent distortion and maintain the integrity of the weld.
- Preheat and post-weld heat treatment: Preheat Inconel before welding is often recommended, especially for thicker materials. This step can reduce the risk of cracking. Similarly, post-weld heat treatment can relieve stress and enhance the weld’s durability.
- Practice safety measures: Inconel welding generates fumes that may be harmful if inhaled. Always ensure proper ventilation and use appropriate personal protective equipment, including a respirator, safety glasses, and heat-resistant gloves.
With these additional tips and tricks, you can confidently weld Inconel and achieve high-quality results.
5 Things You Should Avoid
- Avoid Rushing: Welding Inconel requires patience. Rushing the process could lead to inadequate penetration or other flaws in the weld. Take your time to ensure a quality job.
- Skipping Preheat or Post-Weld Heat Treatment: Never bypass these steps, mainly when dealing with thicker materials. Ignoring these could lead to cracking due to rapid cooling.
- Using Incorrect Filler Materials: Different types of Inconel require specific filler materials. Using the wrong one can weaken the weld or make it prone to defects.
- Ignoring Safety Measures: Pay attention to personal protective equipment or proper ventilation. Exposure to Inconel fumes can be harmful.
- Poor Preparation: Failing to clean the surface of the Inconel or not properly setting up your welding machine can undermine the quality of the weld. Always prepare adequately before starting.
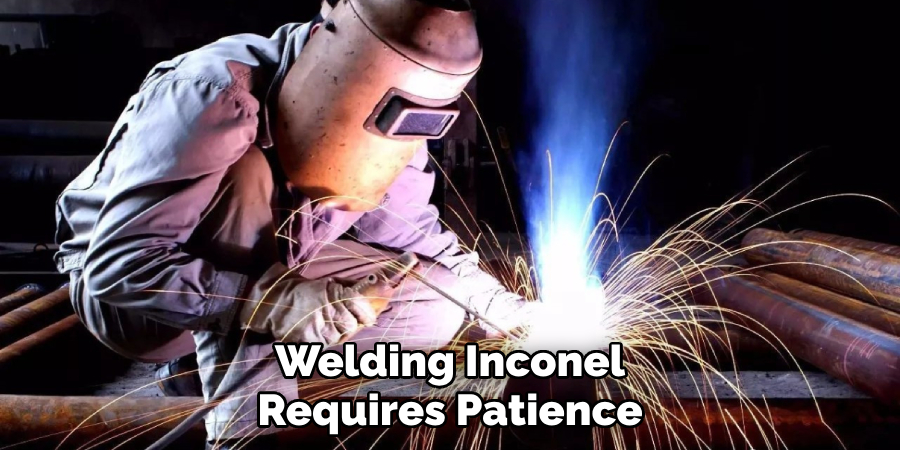
You can ensure a successful Inconel welding experience by avoiding these common mistakes. Remember always to follow safety protocols and take your time to achieve the best results.
Conclusion
As you can see, how to weld inconel requires an experienced eye, steady hands, and a bit of practice. It’s not something that you can just pick up and do in a classroom environment – it needs real-world experience and guidance from a certified welding instructor to become proficient in it. Take the time to research materials, proper shielding, prepping, and cleaning techniques before attempting to weld Inconel.
With the right resources and training, you can be sure that your project results are professional-grade standards. Our goal today is for you to feel confident in learning how to weld safely with Inconel materials.
So find your local welding school or classes online, and get the knowledge and certifications necessary to handle these complex metals confidently. Now, let’s get started on that next project!
Edmund Sumlin is a skilled author for Metal Fixes, bringing 6 years of expertise in crafting a wide range of metal fixtures. With a strong background in metalwork, Edmund’s knowledge spans various types of fixtures, from decorative pieces to functional hardware, blending precision with creativity. His passion for metalworking and design has made him a trusted resource in the industry.
Professional Focus:
- Expert in Metal Fixtures : Edmund aesthetic specializes in creating durable and innovative metal fixtures, offering both appeal and functionality. His work reflects a deep understanding of metalworking techniques and materials.
- Sustainability Advocate : He is dedicated to using sustainable practices, ensuring that every fixture is crafted with eco-friendly methods while maintaining high-quality standards.
In his writing for Metal Fixes, Edmund provides valuable insights into the latest trends, techniques, and practical advice for those passionate about metal fixtures, whether they are professionals or DIY enthusiasts. His focus on combining artistry with engineering helps others discover the true potential of metal in design.