Are you looking to take your car restorations and repairs to the next level? If so, welding sheet metal may be a viable option for some of your projects. Welding can create powerful bonds in metals, making renovations more secure than ever! The good news is welding sheet metal on cars is easier than it seems.
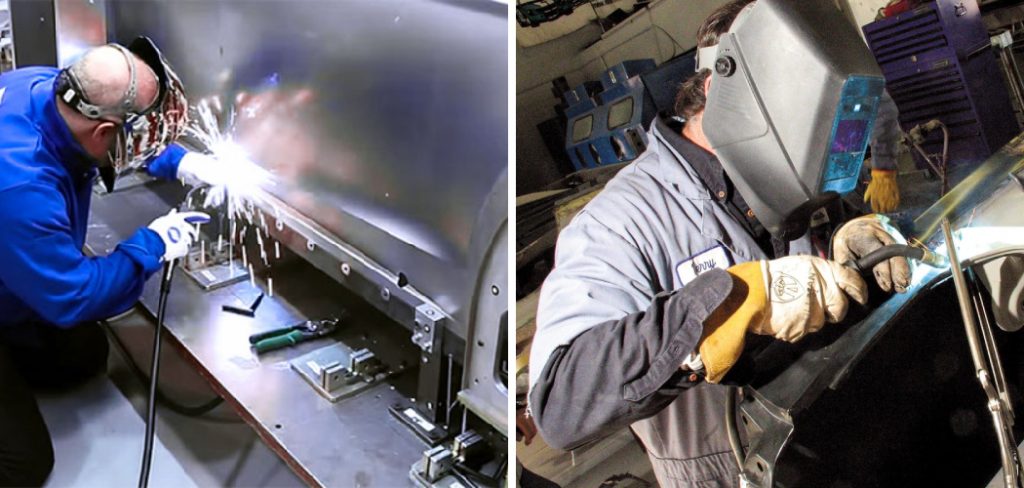
Sheet metal is commonly used for automotive bodywork for its light weight, strength, and flexibility. However, welding sheet metal can be tricky as it is prone to warping or burning if not done correctly. That’s why we have put together a comprehensive guide on how to weld sheet metal on cars so you can confidently tackle any project.
In this blog post, we’ll walk through all the steps necessary to start picking up welding yourself and applying it to car restoration or repair projects.
What Will You Need?
Before you start welding, you must have all the necessary tools and equipment at your disposal. This includes the following:
- Welder: There are several types of welders available, including MIG, TIG, and stick welders. For welding sheet metal on cars, we recommend using a MIG welder.
- Welding Helmet: Protect your eyes with a sturdy welding helmet that can withstand high temperatures and sparks.
- Gloves: Welding gloves provide protection from the intense heat and sparks that come with welding.
- Safety Glasses: Like the helmet, safety glasses protect your eyes from flying debris while welding.
- Clamps: Hold the sheet metal in place while you weld.
- Angle Grinder: An angle grinder can clean up any rough edges or rust on the metal before welding.
- Protective Gear: Welding produces high heat and sparks, so it’s essential to wear protective clothing such as a welding jacket or apron.
Now that you have all the necessary equipment, let’s dive into the steps involved in welding sheet metal on cars.
8 Easy Steps on How to Weld Sheet Metal on Cars
Step 1: Preparation
Start by cleaning the sheet metal. Any paint, rust, or dirt on the surface will interfere with welding and may lead to weak welds. Use your angle grinder or a wire brush to scrub the surface clean. Then, you should align and secure the metal pieces that must be welded together. Use clamps to hold the pieces in place and ensure they are correctly aligned.
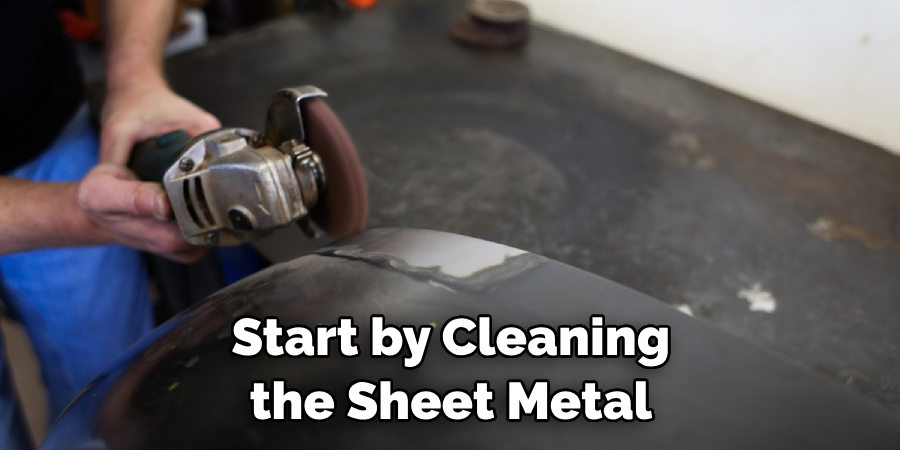
Step 2: Positioning the Welder
After preparing the sheet metal, the next step is setting up your MIG welder. Ensure it’s in a secure position and within a comfortable distance from your work area. Remember to adjust the voltage, wire speed, and gas flow rate according to the thickness of the sheet metal you’re welding. Start with lower settings to avoid burning through the metal, and gradually increase if necessary until you achieve a clean, steady weld. Remember to wear your protective gear before you start welding!
Step 3: Start Welding
Now that everything is set up, you can start welding. Position the welder’s torch at a 45-degree angle to the sheet metal. This position allows the welding wire to join the two pieces of metal effectively. Begin at one end of the seam and slowly move the torch along the line where the two pieces of metal meet.
This process, known as ‘running a bead,’ will create a strong bond between the pieces of metal. Remember to take breaks often to prevent the sheet metal from overheating and warping. When you’ve finished welding, allow the metal to cool naturally. Never plunge hot metal into water to cool it, as this can create stress fractures.
Step 4: Inspection and Cleanup
Once the welded parts have cooled down, it’s time to inspect your work. Look for gaps, holes, or areas that may not have bonded correctly. If you find any, repeat the welding process to fill these in. After a solid, continuous weld, use your angle grinder to smooth out the weld and remove any slag or excess metal.
Be careful not to grind too much, as this could weaken the weld. Always remember to wear safety glasses while grinding to protect your eyes from any flying debris. After sanding, wipe down the welded area with a clean cloth to remove dust or debris. Your newly welded sheet metal is ready for further steps in your car restoration or repair project.
Step 5: Priming and Painting
After cleaning the welded area, it’s time to prime and paint it for added protection and aesthetic enhancement. Start by applying a rust-resistant primer over the weld and surrounding region. Allow the primer to dry completely before moving on to using the paint. Choose a paint color that matches your car’s existing color. Spray the paint evenly over the primed area, ensuring that the weld is completely covered. Allow the paint to dry thoroughly before further work on the car.
Step 6: Regular Maintenance and Checks
After successfully welding sheet metal on your car and painting over it, it’s essential to inspect and maintain the welded areas regularly. Occasionally check for signs of rust or wear. If you spot any, address these issues promptly to prevent them from spreading or worsening. Regular maintenance will ensure the longevity of your car’s bodywork and preserve the integrity of your welding work.
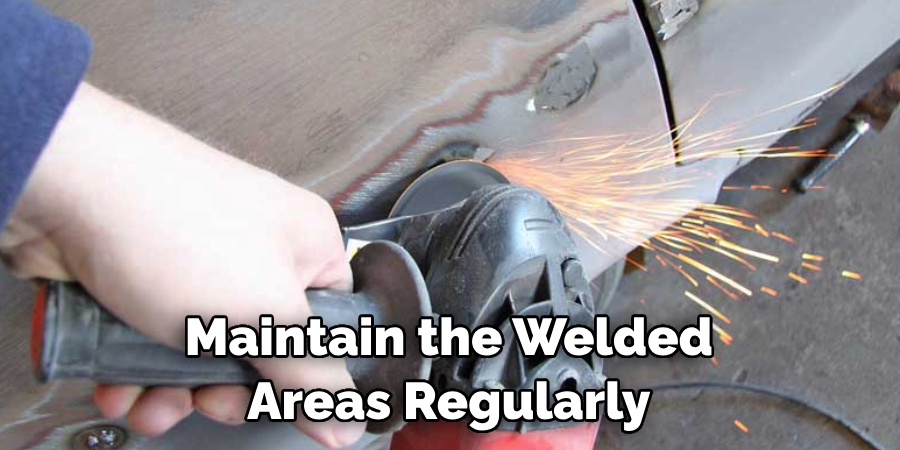
Step 7: Post-Welding Best Practices
Following a successful welding process, it’s crucial to follow some post-welding best practices to ensure the long-term durability of your work. First, always let the metal cool naturally to prevent internal stresses that could compromise the strength of your weld.
Secondly, regularly clean your welding tools and equipment to keep them in optimal condition for future use. This includes the welding gun, clamps, and angle grinder. Finally, continue educating yourself about different welding techniques and materials. The more you know, the more effectively you can weld sheet metal on cars, ensuring the highest quality results.
Step 8: Continuous Learning and Improvement
Building your skills and knowledge in welding continues beyond just one project. Continuous learning and improvement are key to mastering welding sheet metal on cars. Consider attending welding workshops, reading up-to-date materials, or watching online tutorials to enhance your understanding of welding techniques, safety measures, and equipment maintenance. Exploring advanced welding technologies and new materials can also help you improve the quality and efficiency of your welding work.
Following these steps, you can successfully weld sheet metal on cars and achieve professional-looking results.
5 Additional Tips and Tricks
- Practice on Scrap Metal: Before you start welding on your car, it’s beneficial to practice on scrap metal. This helps you get familiar with your welding equipment, perfect your technique, and understand how different metals react to welding.
- Invest in Quality Equipment: While it may seem unnecessary initially, investing in high-quality welding equipment can dramatically improve your results and make the process easier. This includes a good welding helmet for safety, a high-quality MIG welder, and proper clamps for holding your workpiece in place.
- Keep Your Workspace Clean: A clean and organized workspace is safer and can improve your welding results. Keep all tools and materials neatly organized, and ensure that your welding area is free of any flammable materials.
- Use Proper Safety Measures: Welding can be dangerous, so always prioritize safety. Wear protective gear such as gloves, a welding apron, and safety glasses. It’s also essential to have a fire extinguisher nearby in case of any accidents.
- Patience is Key: Welding sheet metal on cars can be a challenging and time-consuming task. Take your time, don’t rush the process, and remember that every mistake is a learning opportunity. With patience and practice, your welding skills will improve over time.
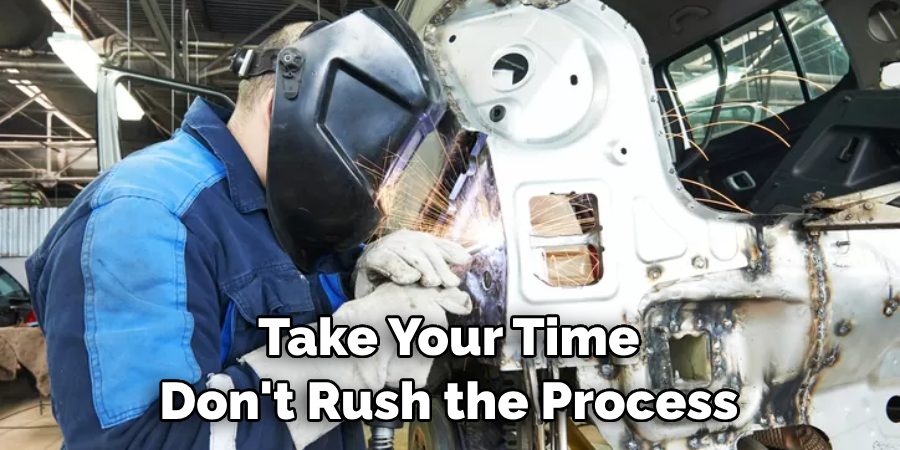
With these additional tips and tricks, you can further enhance your knowledge on welding sheet metal on cars and achieve professional-level results.
5 Things You Should Avoid
- Take Your Time with the Prep Work: Diving straight into the welding process might be tempting, but adequately preparing your materials can lead to good results. Make sure to thoroughly clean and remove any rust or paint on the surface of the metal before welding.
- Take Safety Precautions: Welding can be dangerous if not done correctly. Pay attention to safety measures such as wearing protective gear and ensuring your workspace is well-ventilated.
- Avoid Using Uncalibrated Tools: The precision of your equipment dramatically affects the outcome of your project. Only use tools that have been properly calibrated or maintained.
- Don’t Dismiss Small Mistakes: Even the slightest errors can compromise the overall structural integrity of your welding project. If mistakes happen, rectify them immediately rather than ignoring them.
- Avoid Welding in Poor Conditions: Welding in an area with poor lighting or in inclement weather conditions can lead to subpar work and safety issues. Always ensure your workspace is well-lit and in good condition before welding.
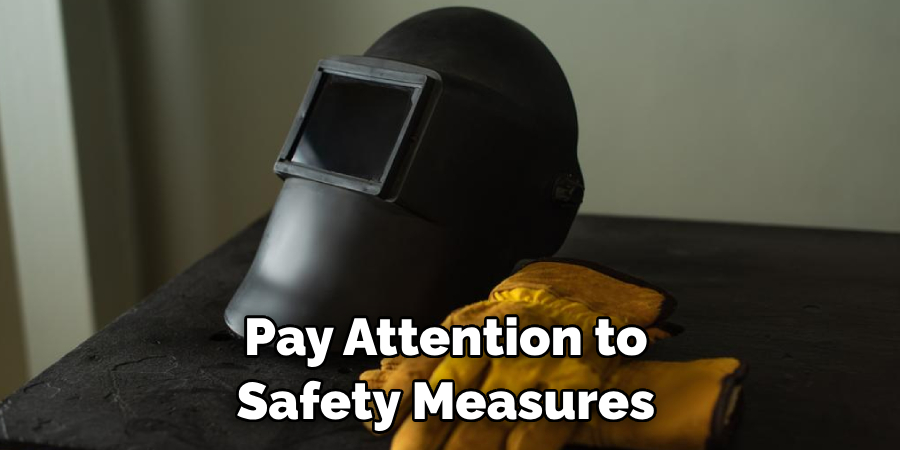
By avoiding these common pitfalls, you increase your chances of successfully welding sheet metal on cars, ensuring the result is functional and aesthetically pleasing.
Conclusion
Safety should always be your priority when welding sheet metal on cars. Use protective gear, mainly goggles and a face shield, to protect your eyes and lungs.
Only attempt any type of welding with proper instruction or supervision. If you are still determining how to weld sheet metal on cars, it is a much better idea to seek assistance from a more experienced welder than trying something on your own that might be risky. Doing so could not only lead to poor outcomes but also health hazards.
Finally, before jumping into it, practice the techniques in this post with some scrap pieces of metal. This will help you gain confidence and insight into the process and make your sheet metal work smoother, more precise, and, most importantly – safe!
Edmund Sumlin is a skilled author for Metal Fixes, bringing 6 years of expertise in crafting a wide range of metal fixtures. With a strong background in metalwork, Edmund’s knowledge spans various types of fixtures, from decorative pieces to functional hardware, blending precision with creativity. His passion for metalworking and design has made him a trusted resource in the industry.
Professional Focus:
- Expert in Metal Fixtures : Edmund aesthetic specializes in creating durable and innovative metal fixtures, offering both appeal and functionality. His work reflects a deep understanding of metalworking techniques and materials.
- Sustainability Advocate : He is dedicated to using sustainable practices, ensuring that every fixture is crafted with eco-friendly methods while maintaining high-quality standards.
In his writing for Metal Fixes, Edmund provides valuable insights into the latest trends, techniques, and practical advice for those passionate about metal fixtures, whether they are professionals or DIY enthusiasts. His focus on combining artistry with engineering helps others discover the true potential of metal in design.