Are you looking for a way to join steel pieces together with ease? Look no further, welding is the perfect answer. It’s an incredibly effective and efficient joining process, especially when it comes to thick metals such as spring steel. Welding spring steel allows for parts of any size and complexity to be seamlessly connected together in one spot. If you’re wondering how welding works or how to weld spring steel yourself, then this blog post is just what you need!
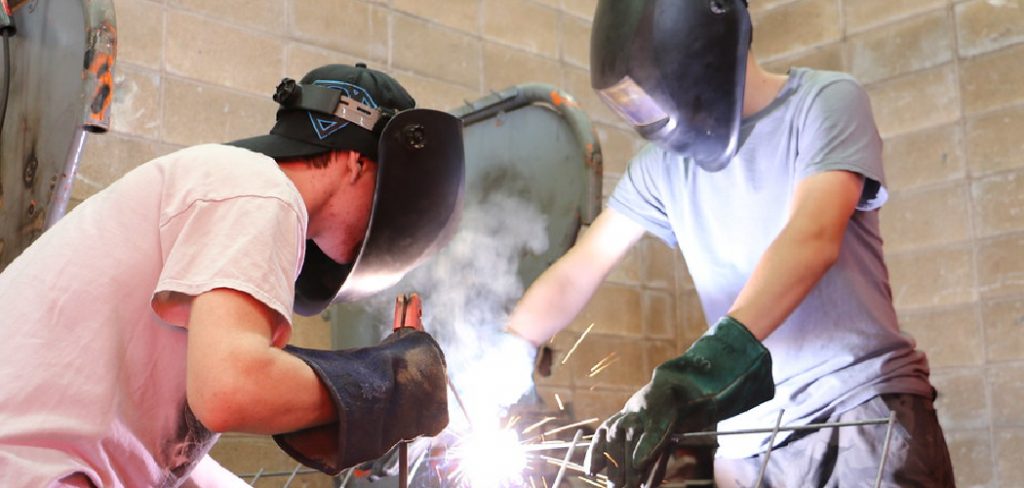
We’ll go over all the basics from safety tips to frequently used equipment so that by the end of this article burying those springs in molten metal will seem like a piece of cake. So get ready – let’s learn about what makes welding and working with spring steels unique!
Safety First
Welding can be a dangerous process; as such, it’s essential to take some necessary safety precautions before starting. Some of the primary safety tips to keep in mind when welding include:
- Protect Your Eyes by Wearing Goggles or a Helmet With Dark Lenses.
- Wear Fire-resistant Clothing and Cover Exposed Skin for Added Protection.
- Keep a Fire Extinguisher Nearby.
- Work in a well-ventilated Area or Use a Respirator to Avoid Inhaling Harmful Fumes.
- Keep Your Workspace Clean and Free of Any Flammable Materials.
Remember, safety should always be a top priority. Make sure to follow all necessary precautions and guidelines before starting any welding project.
Needed Materials
Given below is the list of equipment you’ll need to weld spring steel:
- Welding Machine
- Electrodes (also known as welding rods)
- Protective Gloves and Eyewear
- Hammer or Chisel for slag removal – A welder’s hammer is designed specifically for this purpose and can be found at any hardware store.
- Wire brush or grinder – To remove rust, paint, or mill scale before welding
- Goggles – To protect eyes from harmful UV rays
- Welding helmet – To protect the face and neck from sparks, splatter, and heat burns
Now that we’ve covered everything you’ll need to get started let’s dive into the steps involved in welding spring steel.
11 Step-by-step Guidelines on How to Weld Spring Steel
Step 1: Choose the Right Welding Method
Spring steel is typically welded using either TIG (Tungsten Inert Gas) welding or MIG (Metal Inert Gas) welding. Both methods are suitable for welding spring steel, but each has its unique benefits and challenges. Make sure to choose the method that best suits your project needs. Otherwise, your welding process may become more complicated than it needs to be.
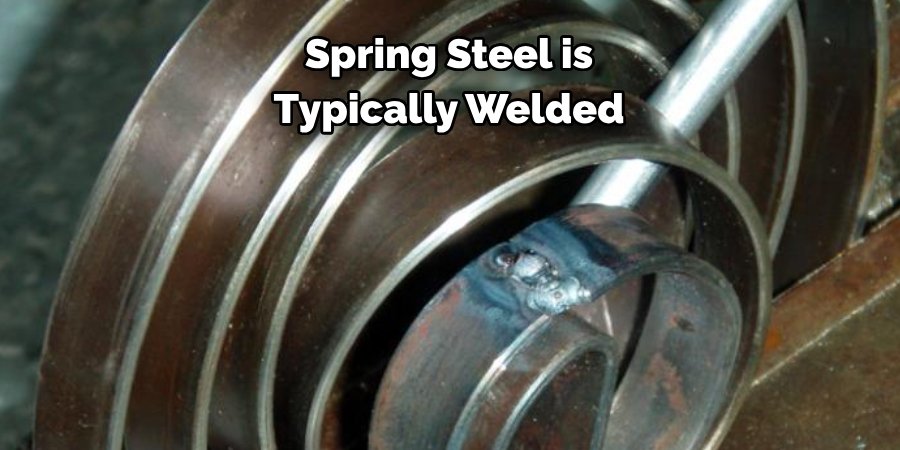
Step 2: Clean the Metal Surface
Before starting, clean the surfaces of the metal parts you want to weld. Use a wire brush or sandpaper to remove an oxidized layer or rust from the steel surface. This will ensure that you have a clean and smooth welding surface for better results. You can also use a degreaser to get rid of any oil or dirt that may have accumulated on the surface.
Step 3: Preheat if Necessary
Some types of spring steel, such as high carbon or alloy steels, may require preheating before welding. This process helps reduce the risk of cracking and enables better weld penetration. Refer to the manufacturer’s instructions or consult a professional welder to determine if preheating is necessary for your specific spring steel material.
Step 4: Choose the Right Filler Material
Selecting the right filler material is crucial when welding spring steel. Typically, low carbon content, mild steel filler rods are recommended for welding these types of steel. Match the rod diameter with the base metal thickness for optimal results. It’s also essential to use clean filler rods for the best weld quality.
Step 5: Set Up Your Welding Equipment
Ensure that your welding machine is set to the appropriate settings for the type and thickness of spring steel you are working with. The recommended settings may vary depending on the welding method being used, so make sure to check the manufacturer’s instructions or consult a professional welder. You should also check the gas flow rate and wire speed for MIG welding. But for TIG welding, make sure to sharpen your tungsten electrode before starting.
Step 6: Choose Your Welding Technique
Depending on the shape and size of your project, you may need to apply different welding techniques. For example, TIG welding is often used for smaller and more intricate projects, while MIG welding is suitable for larger and more straightforward projects. Whichever method you choose, make sure your technique is consistent throughout the welding process.
Step 7: Start Welding
Place the metal parts in their designated positions and begin welding. Make sure to use a steady hand and move at a constant speed to ensure even weld penetration. Use the correct angle of the welding torch and maintain the recommended distance between the torch and the metal surface. Weld across the entire joint, making sure to fill any gaps or holes as you go along.
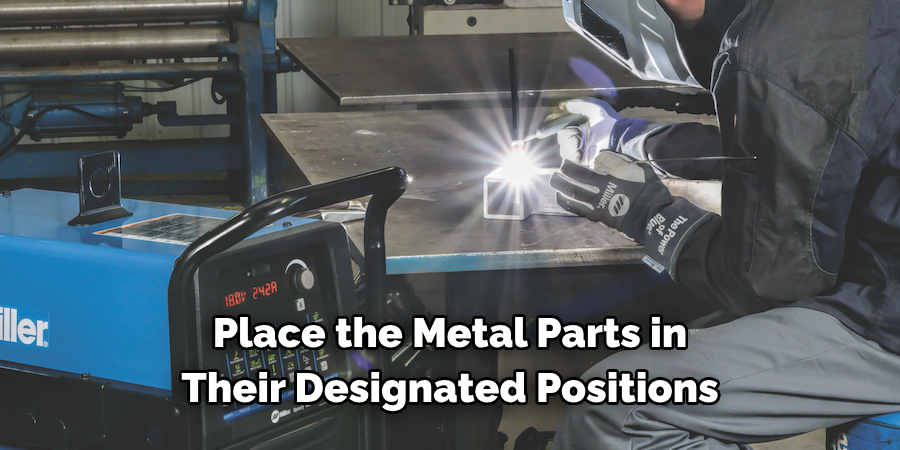
Step 8: Control Heat Input
Controlling heat input is crucial when welding spring steel. Too much heat can lead to cracks, while too little heat may result in an incomplete weld. Monitor your welding machine settings and adjust as necessary to maintain the optimal heat input. You may also need to pause and allow the metal to cool down if it becomes too hot.
Step 9: Repeat for Multiple Passes
In some cases, a single pass may not be enough to achieve the desired weld strength. If this is the case, make additional passes over the joint until the desired weld strength is achieved. Make sure to let each pass cool down before adding another layer. Otherwise, the heat buildup can cause warping or cracking.
Step 10: Clean and Finish
Once you have completed all the necessary welding, allow the metal to cool down completely. Once cooled, use a wire brush or sandpaper to clean off any slag or spatter that may have formed on the surface. You can also use a grinder or file to smooth out any rough edges and achieve a clean, finished look. It is crucial to get rid of any sharp edges, as they can pose a hazard.
Step 11: Post-weld Heat Treatment
In some cases, it may be necessary to perform post-weld heat treatment to reduce the risk of cracking and improve the overall weld strength. This process involves heating the welded metal to a specific temperature and then allowing it to cool slowly. The exact time and temperature required may vary depending on the type of spring steel being welded, so make sure to consult a professional welder for guidance.
Following these guidelines and taking necessary precautions will ensure a successful and safe welding experience when working with spring steel. Remember to always prioritize safety, cleanliness, and proper technique for the best results. Now that you know how to weld spring steel, you can confidently take on any project involving this versatile material. Happy welding!
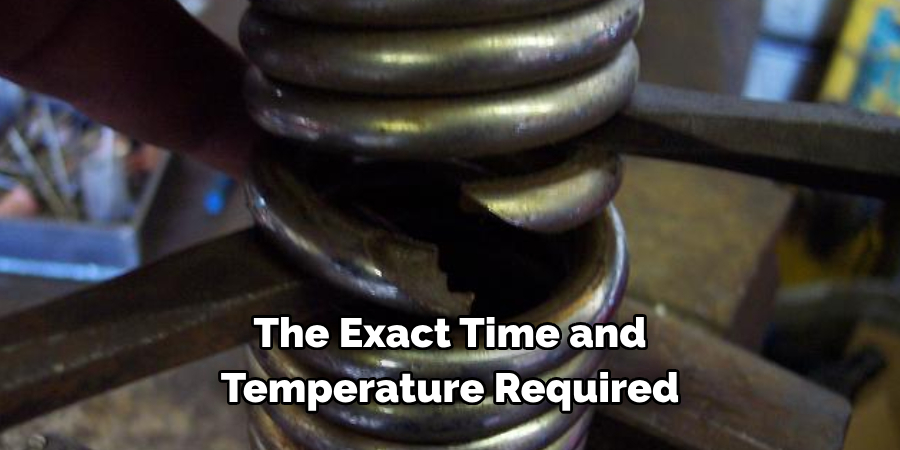
Additional Tips and Considerations
- Always wear appropriate safety gear when welding, including gloves, eye protection, and a welding mask.
- If possible, practice on scrap pieces of spring steel before starting your project to get a feel for the welding process.
- Be aware that different types of spring steel may have varying levels of weldability. Consult with a professional or test welds beforehand if unsure.
- Make sure the welding area is well-ventilated to prevent inhaling fumes and gases produced during the welding process.
- If you encounter any difficulties or are unsure about a specific step, do not hesitate to seek guidance from a professional welder. Safety should always be the top priority when welding. Additionally, it is crucial to be mindful of the potential hazards and risks associated with welding spring steel. These include:
- The risk of electric shock if proper safety measures are not followed.
- Exposure to harmful fumes and gases produced during the welding process can cause respiratory problems.
- Fires and explosions if welding near flammable materials or in a confined space.
- Eye injuries from sparks and debris flying off during welding. Make sure to wear proper eye protection at all times.
- Burns from hot metal surfaces or molten metal splatter. Wear heat-resistant gloves and clothing to protect yourself.
Frequently Asked Questions
Q1. Can I Weld Spring Steel Using an Oxy-acetylene Torch?
A1. Yes, you can weld spring steel using an oxy-acetylene torch, but this method is not as commonly used as MIG or TIG welding due to the potential for heat distortion and warping of the metal.
Q2. Is Preheating Required for Welding Spring Steel?
A2. It is generally recommended to preheat the metal before welding spring steel to minimize heat distortion and reduce the risk of weld cracking. However, this may not always be necessary depending on the type and thickness of the steel being welded.
Q3. Can I Weld Different Types of Spring Steel Together?
A3. Yes, you can weld different types of spring steel together, but it is important to consider the compatibility and properties of each type beforehand to ensure a strong and successful weld. It is always best to consult with a professional if unsure.
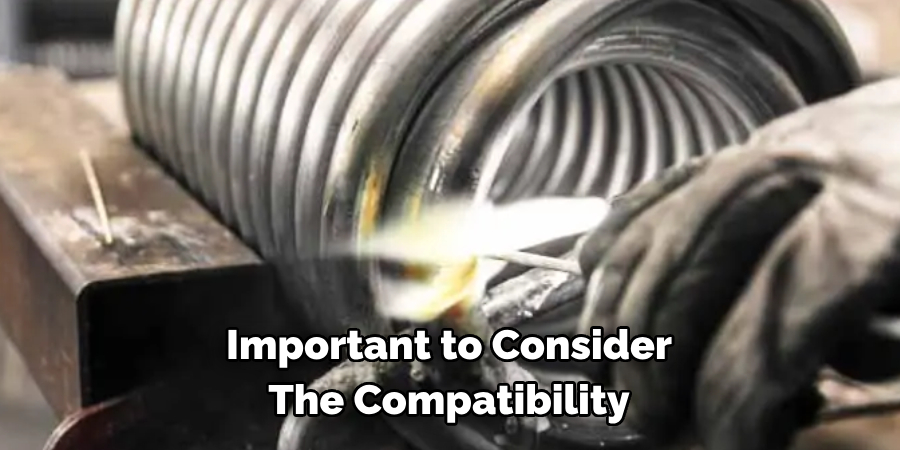
Conclusion
Finally, by following the steps outlined in this blog post, you will be able to master welding spring steel quickly and efficiently. This skill can come in handy for a variety of projects, from crafting art pieces to creating furniture and more. It is an undertaking involving precision and excellent workmanship– so don’t be shy about investing some time into garnering some practice experience with the techniques shown here on how to weld spring steel.
Whether you are involved with hobby welding or are a professional metalworker, try your hand at welding spring steel today and reap the rewards of your creation tomorrow! Already experienced in this craft? Share your expertise with others in our online forums and help keep the tradition of skilled craftsmen alive and vibrant.
Edmund Sumlin is a skilled author for Metal Fixes, bringing 6 years of expertise in crafting a wide range of metal fixtures. With a strong background in metalwork, Edmund’s knowledge spans various types of fixtures, from decorative pieces to functional hardware, blending precision with creativity. His passion for metalworking and design has made him a trusted resource in the industry.
Professional Focus:
- Expert in Metal Fixtures : Edmund aesthetic specializes in creating durable and innovative metal fixtures, offering both appeal and functionality. His work reflects a deep understanding of metalworking techniques and materials.
- Sustainability Advocate : He is dedicated to using sustainable practices, ensuring that every fixture is crafted with eco-friendly methods while maintaining high-quality standards.
In his writing for Metal Fixes, Edmund provides valuable insights into the latest trends, techniques, and practical advice for those passionate about metal fixtures, whether they are professionals or DIY enthusiasts. His focus on combining artistry with engineering helps others discover the true potential of metal in design.