Welding thin metal poses a unique set of challenges, requiring a delicate balance between heat application and precision to avoid warping or burn-through. Whether you’re working with sheet metal, thin tubing, or other lightweight materials, the key to successful welding lies in mastering the nuances of technique and equipment settings. In this comprehensive guide, we delve into how to weld thin metal, offering insights and practical tips for welders of all skill levels.
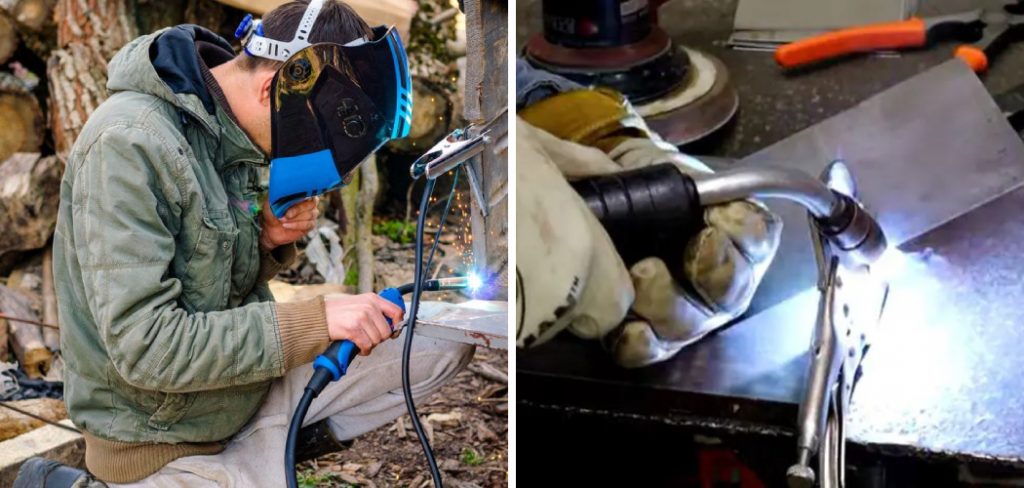
From selecting the appropriate welding process, such as TIG or MIG, to adjusting heat settings and employing proper filler materials, readers will gain valuable knowledge on navigating the intricacies of welding thin-gauge metals. Join us as we explore the essential considerations and step-by-step procedures to achieve clean, strong, and precise welds on thin metal, ensuring the integrity and durability of your welded projects.
Importance of Welding Thin Metal
Welding is an essential process in metal fabrication, used to join two or more pieces of metal together. It is a critical skill for any metalworker, as it allows for the creation of durable and structurally sound structures. However, welding thin metal requires a different set of techniques and considerations compared to thicker metals.
Thin metal refers to any sheet metal that is less than 3/16 inch thick. This includes materials such as aluminum, stainless steel, and other common metals used in various industries. Welding thin metal requires a high level of precision and control to ensure the integrity and strength of the welded joint.
One of the main challenges in welding thin metal is the potential for warping or distortion during the process. Due to its thinner nature, thin metal is more susceptible to heat and can easily become deformed or bent if not welded properly. This could compromise the structural integrity of the final product.
Another important consideration when welding thin metal is the type of welding technique used. In general, TIG (Tungsten Inert Gas) welding is the preferred method for thinner materials as it provides better control over the heat input and allows for precise welding.
10 Methods How to Weld Thin Metal
1. Gas Metal Arc Welding (GMAW)
Gas metal arc welding, also known as GMAW or MIG welding, is one of the most popular methods for welding thin metal. This method uses an electrical current to create an electric arc between the base metal and a consumable wire electrode.
The heat generated by the arc melts both the wire and the base metal, allowing them to fuse together. GMAW is relatively easy to learn and can be used on a variety of metals, including aluminum and stainless steel.
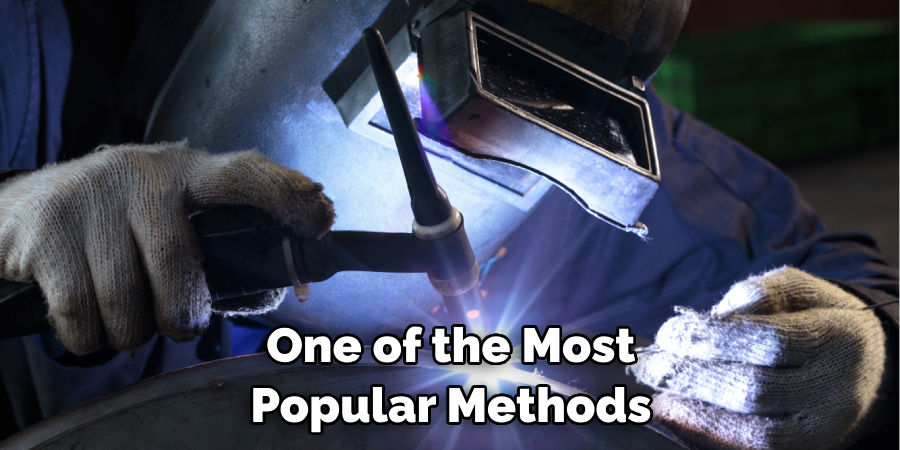
2. Shielded Metal Arc Welding (SMAW)
Shielded metal arc welding, also known as SMAW or stick welding, is a popular method for welding thin metal. This method uses an electrical current to create an electric arc between the base metal and a consumable electrode covered in flux. The heat generated by the arc melts both the electrode and the base metal, allowing them to fuse together. SMAW is relatively easy to learn but requires more skill than GMAW when working with thin metals.
3. Tungsten Inert Gas (TIG) Welding
Tungsten inert gas welding, also known as TIG or GTAW welding, is another popular method for welding thin metal. This method uses an electrical current to create an electric arc between the base metal and a non-consumable tungsten electrode.
The heat generated by the arc melts both the tungsten electrode and the base metal, allowing them to fuse together. TIG welding is more difficult than other methods but provides better control over welds when working with thin metals.
4. Oxy-Acetylene Welding
Oxy-acetylene welding is a method that uses fuel gases such as acetylene and oxygen to generate heat for joining metals together. This method works well on thin metals because it allows for precise temperature control with minimal distortion of the workpiece due to its low thermal mass.
Additionally, oxy-acetylene can be used on almost any type of material due to its high-temperature capabilities and versatility in terms of joint designs that can be created with it.
5. Plasma Arc Welding (PAW)
Plasma arc welding is another popular method for welding thin metals that utilize plasma gas instead of traditional fuel gases like acetylene or propane to generate heat for joining two pieces together. This process provides higher levels of accuracy when working with thinner materials because it creates less distortion due to its lower thermal mass compared to other methods like oxy-acetylene or shielded metal arc welding (SMAW).
6. Laser Beam Welding
Laser beam welding is a specialized form of fusion joining that utilizes a highly focused laser beam along with filler material in order to join two pieces together without melting away too much material from either surface being joined together.
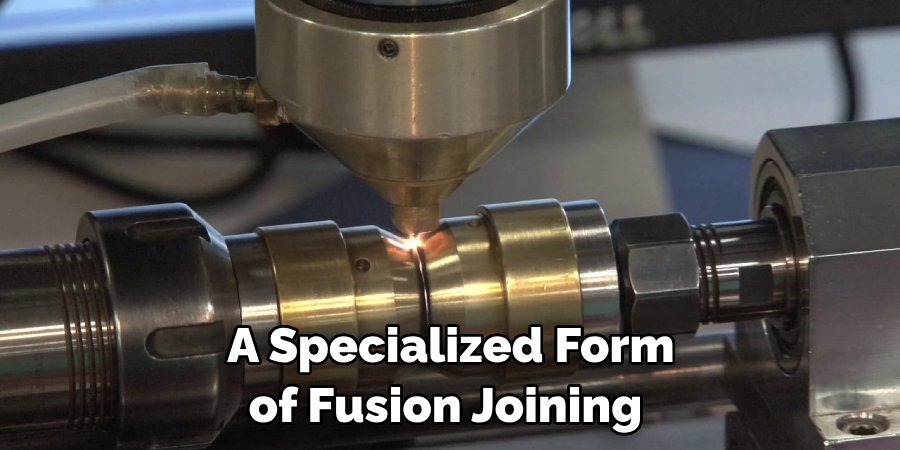
Laser beam welds are often preferred when working with thinner materials because they provide higher levels of accuracy while still maintaining strength in joints created through this process. Additionally, laser beam welds do not require additional filler material, which helps reduce costs associated with this process.
7. Electron Beam Welding
Electron beam welding is similar in principle to laser beam welding but utilizes electrons instead of light waves in order to create welds between two pieces being joined together. Electron beams are able to produce higher levels of energy than lasers, which makes this process ideal when working with thicker materials but still applicable when working with thinner materials as well.
8. Ultrasonic Welding
Ultrasonic welding utilizes high-frequency sound waves combined with pressure in order to join two pieces together without creating too much distortion from excessive amounts of heat during this process. Ultrasonic welds are often preferred when working with thinner materials because they provide higher levels of accuracy while still maintaining strength in joints created through this process.
9. Friction Stir Welding
Friction stir welding utilizes friction generated from rotating tools combined with pressure in order to join two pieces together without creating too much distortion from excessive amounts of heat during this process.
Friction stir welds are often preferred when working with thinner materials because they provide higher levels of accuracy while still maintaining strength in joints created through this process. Additionally, friction stir welds do not require additional filler material, which helps reduce costs associated with this process.
10. Spot Welding
Spot welding is a specialized form of resistance welding that utilizes pressure along with an electrical current to create welds between two pieces. This method works well on thin metals because it allows for precise control over the location and size of the weld due to its use of electrodes.
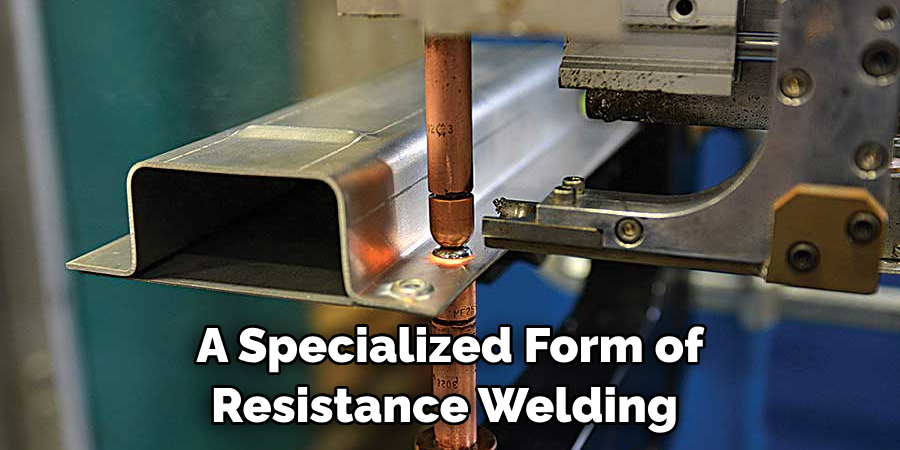
Additionally, spot welding can be done quickly and efficiently, making it a cost-effective option for joining thin metal pieces together. However, it may not be as strong as other welding methods and is typically used for temporary or non-load-bearing applications.
Things to Consider When Welding Thin Metal
Welding thin metal can be a challenging task, but with the right techniques and considerations, it can be done successfully. Here are some important things to keep in mind when welding thin metal:
Choose the Right Welding Process:
The first thing to consider when welding thin metal is selecting the appropriate welding process. The most common processes for thin metal welding are TIG (Tungsten Inert Gas) and MIG (Metal Inert Gas).
TIG welding is ideal for thin metals as it offers precise control over the heat input, which is essential for preventing warping or burn-through. On the other hand, MIG welding may be suitable for thicker metal but can also be used for thin metal if proper settings and techniques are applied.
Use the Correct Filler Material:
Another crucial factor in welding thin metal is using the right filler material. The filler material should have a lower melting point than the base metal to avoid overheating and creating holes or distortion. For example, when welding stainless steel, it is recommended to use a lower melting point filler such as 309L instead of 308L.

Clean and Prepare the Metal:
Before beginning the welding process, it is essential to clean and prepare the metal surface thoroughly. Any contaminants or debris on the surface can cause defects in the weld, leading to weaker joints. Use a wire brush or solvent to remove any dirt, oil, or rust from the surface before welding.
Conclusion
Welding thin metal can be intimidating at first – but it doesn’t have to be! With the right tools, techniques and safety precautions, you can successfully weld even the thinnest sheets of metal. Working with thinner materials also gives you more room for creativity as special pieces that don’t require a lot of structural strength can easily be added into your project.
To get started, make sure to equip yourself with the best quality low-heat welding tools in order to achieve the perfect weld and practice until you feel confident in your abilities. And remember, safety should always come first – so take all the necessary steps to prevent accidents while developing your welding skills with thin metal. Now that you know how to weld thin metal correctly, go ahead and get creative with your projects!
Edmund Sumlin is a skilled author for Metal Fixes, bringing 6 years of expertise in crafting a wide range of metal fixtures. With a strong background in metalwork, Edmund’s knowledge spans various types of fixtures, from decorative pieces to functional hardware, blending precision with creativity. His passion for metalworking and design has made him a trusted resource in the industry.
Professional Focus:
- Expert in Metal Fixtures : Edmund aesthetic specializes in creating durable and innovative metal fixtures, offering both appeal and functionality. His work reflects a deep understanding of metalworking techniques and materials.
- Sustainability Advocate : He is dedicated to using sustainable practices, ensuring that every fixture is crafted with eco-friendly methods while maintaining high-quality standards.
In his writing for Metal Fixes, Edmund provides valuable insights into the latest trends, techniques, and practical advice for those passionate about metal fixtures, whether they are professionals or DIY enthusiasts. His focus on combining artistry with engineering helps others discover the true potential of metal in design.