Determining whether a screw is stainless steel is essential for projects requiring corrosion resistance and durability.
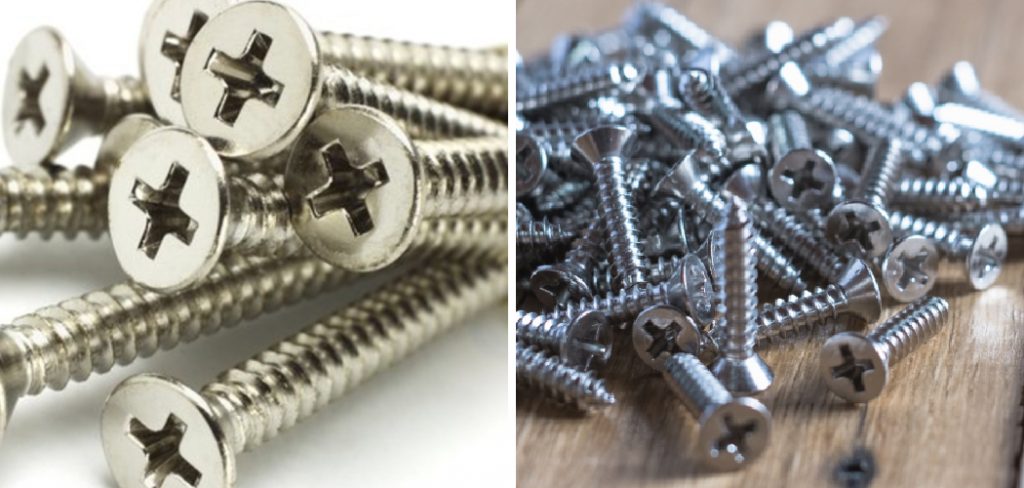
Stainless steel screws offer superior strength and resilience against rust, making them ideal for outdoor and marine applications. Identifying stainless steel screws involves examining their appearance and magnetic properties. Unlike regular steel, stainless steel screws typically exhibit a non-magnetic quality due to their composition.
Additionally, they feature a shiny, metallic finish that resists tarnishing and rusting over time. Whether you’re a hobbyist or professional, understanding how to distinguish stainless steel screws ensures you select the right fasteners for long-lasting results in construction, automotive repairs, or any project where environmental conditions are a concern.
This guide will outline methods and tips for how to tell if a screw is stainless steel, ensuring optimal performance and reliability in your applications.
Importance of Identifying Stainless Steel
Identifying stainless steel is crucial for a variety of reasons. First and foremost, the distinctive properties of stainless steel make it a preferred choice for environments exposed to moisture, chemicals, and varying weather conditions. Its corrosion resistance helps prevent the degradation of structures and products, ultimately extending their lifespan and reducing maintenance costs.
Moreover, stainless steel is known for its strength and durability, which provides additional safety, especially in critical applications such as building construction, automotive engineering, and medical instruments.
Using the correct type of steel ensures that the integrity of the project is not compromised, thus protecting both the investment and the safety of individuals who rely on these structures and devices.
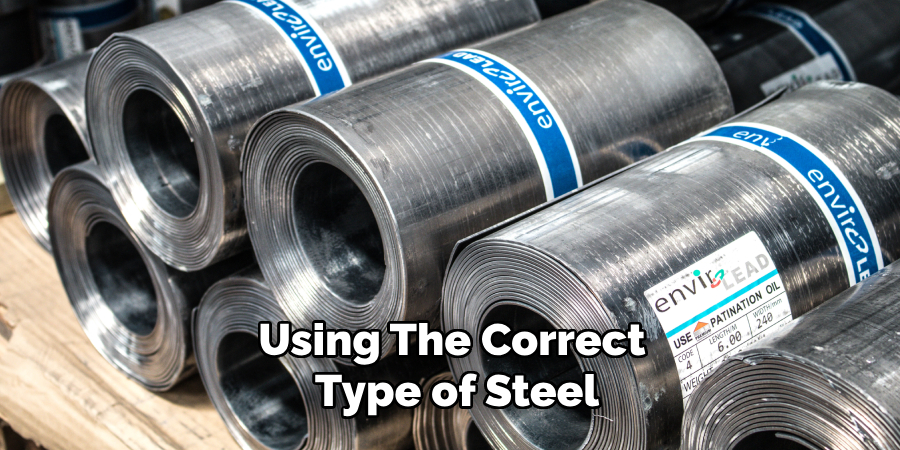
Therefore, correctly identifying stainless steel is a vital skill for anyone involved in construction, repairs, or manufacturing.
Benefits of Using Stainless Steel Screws
Stainless steel screws offer a multitude of benefits that enhance the quality and longevity of your projects. One of the primary advantages is their exceptional corrosion resistance.
Unlike regular steel screws, stainless steel screws are resistant to rust and oxidation, making them ideal for both indoor and outdoor applications, including environments exposed to moisture, salt, or chemicals.
This durability ensures that structures and fixtures remain secure and intact over time, reducing the need for frequent maintenance or replacements.
Moreover, stainless steel screws possess superior strength and toughness. They can withstand significant mechanical stress without deforming or breaking, providing reliable performance in demanding conditions. This robustness is critical in construction, automotive repairs, and marine applications where safety and integrity are paramount.
In addition to their functional benefits, stainless steel screws have an aesthetic appeal due to their shiny, polished finish.
They maintain their appearance without tarnishing, contributing to the overall look of the project. This is particularly advantageous in visible applications where both functionality and appearance are crucial.
10 Methods How to Tell if a Screw Is Stainless Steel
1. Visual Examination:
Initiate your assessment by closely observing the screw’s surface characteristics. Stainless steel screws typically boast a lustrous, metallic sheen ranging from a subdued silver to a gleaming polish.
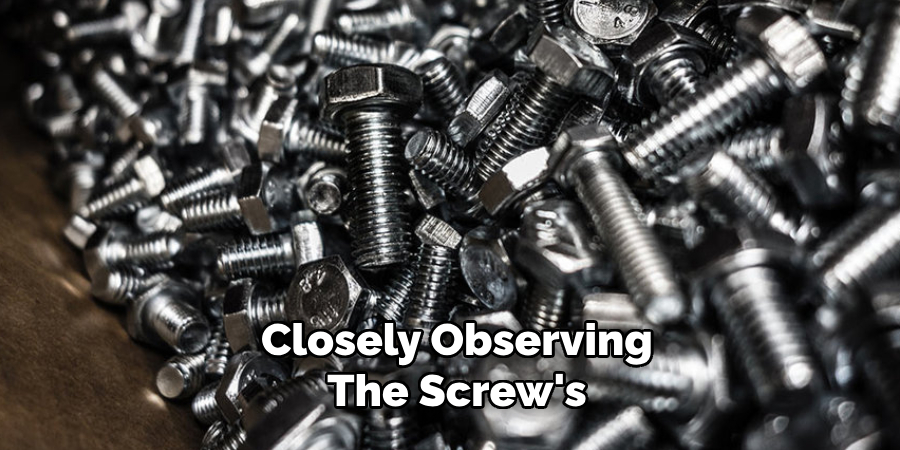
This visual cue often lacks the tarnish or discoloration commonly found on other metals prone to oxidation.
2. Magnet Test:
Utilize a magnet to gauge the magnetic response of the screw. Stainless steel, owing to its non-ferrous nature, generally exhibits minimal attraction to magnets.
However, certain stainless steel alloys may possess slight magnetic properties due to varying compositions, necessitating careful interpretation of magnetism as a preliminary indicator.
3. Corrosion Resistance:
Assess the screw’s resistance to corrosion, a hallmark of stainless steel’s durability. Exposure to moisture or harsh environmental conditions typically leaves stainless steel screws unblemished by rust or corrosion. Their resilience underscores their suitability for applications requiring prolonged outdoor exposure or contact with corrosive substances.
4. Material Markings:
Scrutinize the screw for any identifying marks, often engraved or stamped on the head or shaft.
Look for abbreviations such as “SS” denoting stainless steel, or alphanumeric codes like “A2” and “A4” indicating specific grades of stainless steel recognized for their corrosion resistance and composition.
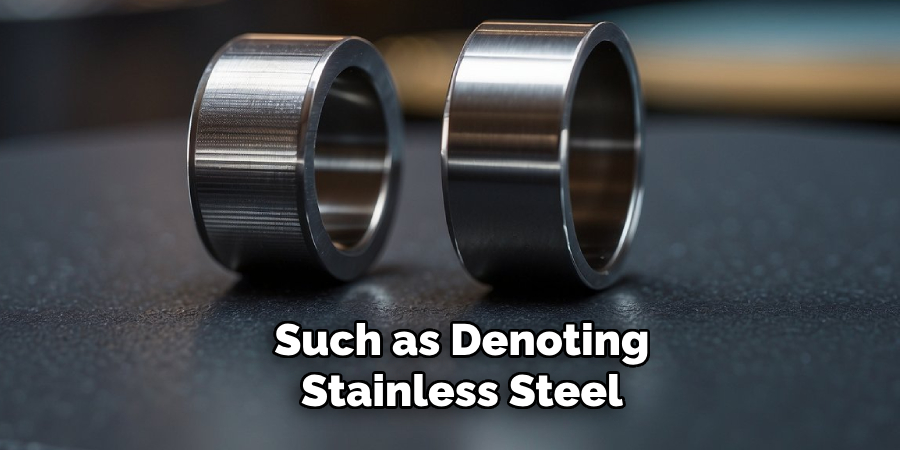
5. Acid Test:
Employ a diluted nitric acid solution, typically around 10% concentration, to conduct a more advanced test.
Apply a small amount of acid to an inconspicuous area of the screw and observe the reaction. Genuine stainless steel will demonstrate minimal to no reaction, reaffirming its resistance to acid corrosion. Exercise caution and follow safety protocols when handling acids.
6. Weight Comparison:
Conduct a comparative assessment of the screw’s weight against that of known carbon steel counterparts.
Stainless steel, characterized by its lower density relative to carbon steel, typically feels lighter when held. This method provides a tactile means to distinguish stainless steel screws amidst a variety of metal fasteners.
7. Spark Test:
Employ a grinder or abrasive wheel to initiate a spark test, a technique commonly used in industrial settings. Observing the sparks generated during grinding can offer valuable insights: stainless steel produces short, reddish sparks due to its chromium and nickel content, distinct from the longer, yellow sparks emitted by carbon steel.
8. Spectrometer Analysis:
For precise and scientific verification, employ a handheld spectrometer capable of analyzing the elemental composition of the screw. Stainless steel is characterized by specific proportions of chromium and nickel, pivotal in differentiating it from other metallic alloys through spectroscopic analysis.
9. Consultation with Manufacturer Specifications:
Refer to manufacturer-provided specifications or documentation if available.
Many reputable manufacturers furnish comprehensive details regarding their products, including material composition and grade classifications, facilitating informed identification of stainless steel screws for diverse applications.
10. Professional Testing Services:
When absolute certainty is paramount, consider engaging professional testing services equipped with spectroscopy or chemical analysis capabilities.
These accredited laboratories offer rigorous assessments to definitively ascertain whether a screw conforms to stainless steel standards, ensuring compliance with stringent quality and performance requirements.
Things to Consider When Selecting Stainless Steel Screws
Application Environment
The environment in which the screws will be used plays a critical role in the selection process.
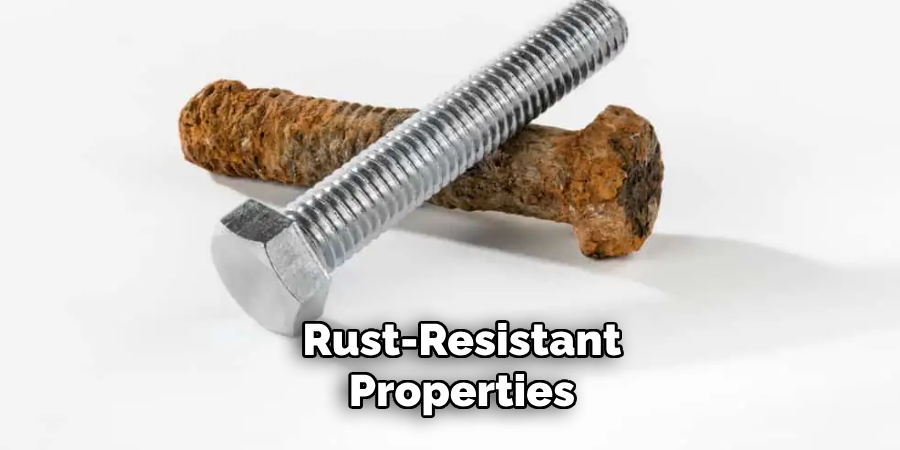
Stainless steel screws are ideal for areas prone to moisture, salt exposure, or corrosive chemicals due to their rust-resistant properties. However, consider the specific grade of stainless steel required for maximum effectiveness in different environments, such as marine settings or high-temperature conditions.
Load and Stress Requirements
Understanding the mechanical demands of your project is crucial. Different grades of stainless steel exhibit varying levels of strength and toughness. For high-stress applications, such as structural and automotive uses, selecting screws that can withstand significant mechanical stress without deforming or breaking is essential.
Compatibility with Other Materials
Consider the types of materials the stainless steel screws will come into contact with. Some materials may cause galvanic corrosion when in contact with stainless steel, affecting the integrity of both components. Ensure compatibility to prevent any long-term damage or compromise to the structure.
Screw Size and Design
The dimensions and design of the screw must align with the requirements of the project. This includes the length, diameter, thread type, and head shape. Proper sizing ensures that the screws serve their intended purpose without the risk of overloading or structural failure.
Aesthetic Considerations
For projects where appearance is important, the aesthetic qualities of the screw are just as significant as its functional attributes. Stainless steel screws come with a polished finish that resists tarnishing, making them suitable for visible applications where a clean and professional look is desired.
Common Mistakes to Avoid
Using the Wrong Grade of Stainless Steel
One of the most common mistakes is selecting the incorrect grade of stainless steel for a specific application. Different grades offer varying resistance to corrosion, heat, and mechanical stress. Choosing a grade that is unsuitable for the environmental conditions can lead to premature failure of the screws.
Over-tightening Screws
Over-tightening stainless steel screws can cause stripping of the threads, breakage, or damage to the material being fastened. It’s important to use the right torque settings and tools to ensure that screws are fastened securely without exceeding their mechanical limits.
Ignoring Galvanic Corrosion
When stainless steel screws are used in conjunction with dissimilar metals, galvanic corrosion can occur. This electrochemical process can compromise both the screw and the material it fastens. Always ensure material compatibility and consider using isolation materials or coatings to mitigate this risk.
Neglecting Pre-drilling
Failure to pre-drill holes for stainless steel screws can lead to splitting of the material, misalignment, or improper seating of the screw. Pre-drilling ensures that the screw can penetrate the material without causing damage and maintains structural integrity.
Using Low-Quality Screws
Opting for low-quality or counterfeit stainless steel screws can result in subpar performance and durability issues. Always source screws from reputable manufacturers and verify their certifications to avoid unexpected failures and costly repairs.
Conclusion
Selecting the right stainless steel screws for your project is a meticulous process that involves various considerations.
From identifying the correct material through tests and markings to assessing the specific requirements of your application environment, load stress, and material compatibility, each step plays a vital role in ensuring the success and longevity of your installation.
Additionally, paying attention to aesthetic attributes, compliance with industry standards, and economic factors like cost and availability can further streamline the selection process. Be sure to follow all instructions on how to tell if a screw is stainless steel carefully, and always consult an expert when in doubt.
Edmund Sumlin is a skilled author for Metal Fixes, bringing 6 years of expertise in crafting a wide range of metal fixtures. With a strong background in metalwork, Edmund’s knowledge spans various types of fixtures, from decorative pieces to functional hardware, blending precision with creativity. His passion for metalworking and design has made him a trusted resource in the industry.
Professional Focus:
- Expert in Metal Fixtures : Edmund aesthetic specializes in creating durable and innovative metal fixtures, offering both appeal and functionality. His work reflects a deep understanding of metalworking techniques and materials.
- Sustainability Advocate : He is dedicated to using sustainable practices, ensuring that every fixture is crafted with eco-friendly methods while maintaining high-quality standards.
In his writing for Metal Fixes, Edmund provides valuable insights into the latest trends, techniques, and practical advice for those passionate about metal fixtures, whether they are professionals or DIY enthusiasts. His focus on combining artistry with engineering helps others discover the true potential of metal in design.